The 3D Printed Electric Skateboard (With Genius Doug Smith)
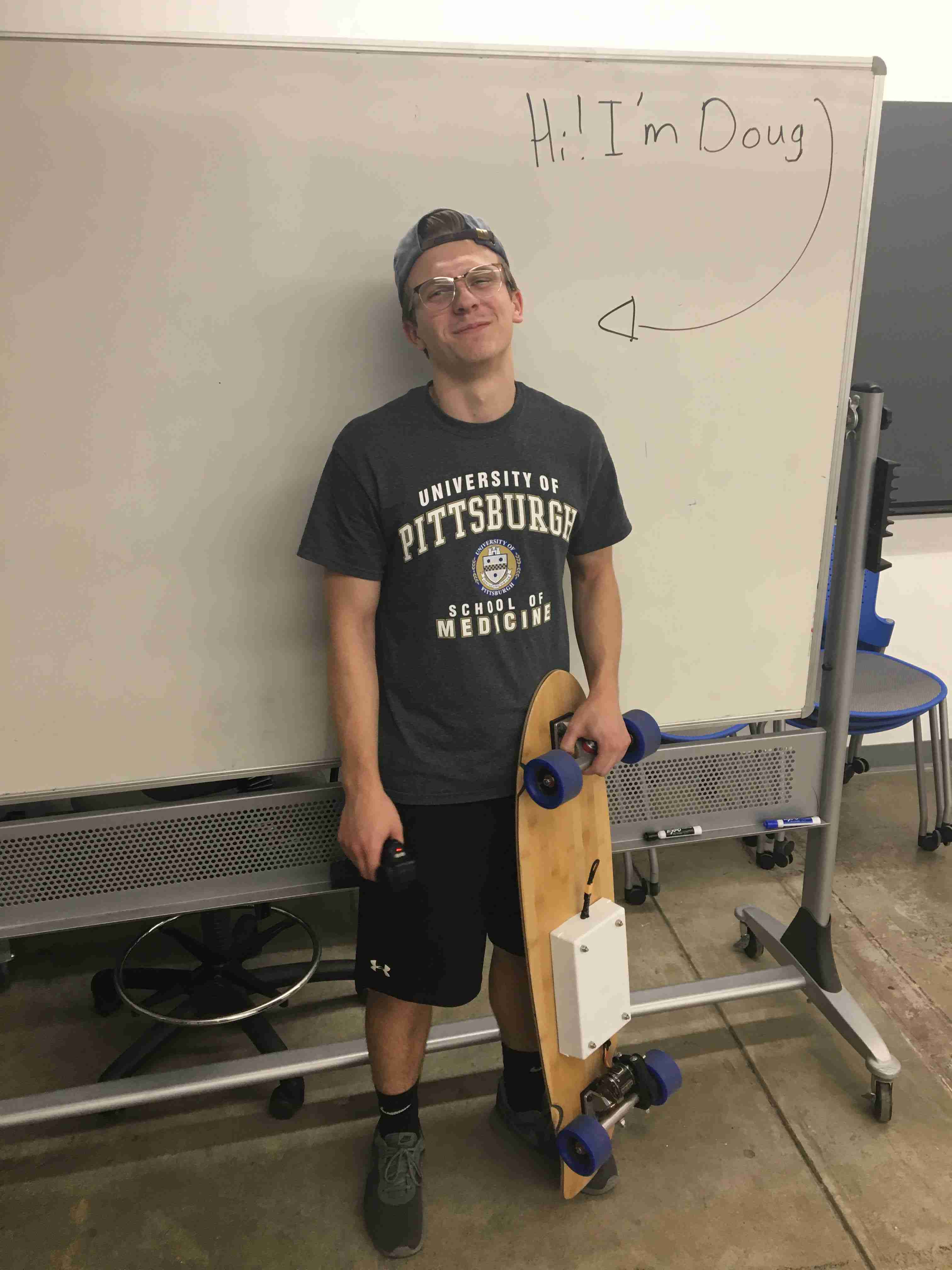
STILL IN PROGRESS: CAD files will be available soon =).
Inspiration
Electric skateboards can cost up to $600-$700 for the most basic setups. Even if you have a DIY skateboard,
it's very difficult to build a quality electric skateboard without access to a machine shop or a couple weeks of work.
My hope with this was to build a high quality, reliable skateboard with only 6 hours of assembly for under $350. This reaches 18 mph.
This would require the useage of 3D printed parts, but the eskateboard community's pieces often broke, so I wanted to through my engineering hat into the ring and see if I could do better.
Basically, we built an electric skateboard that requires nothing more complicated than a 3D printer, a drill, and a soldering iron, common tools for hackers.
How does it work?
Note: A lot of this is reposted from my original 25mph electric skateboard.
There are three ways of doing this:
- You can weld the motor mount to the axle. Best way, but lots of work if you don't have a welder.
- You can clamp the motor mount to the axle by screwing two pieces of aluminum around the axle as seen here . Sounds good, but it's expensive.
- You can drill through the axle and the piece of aluminum and hold it in place. Sounds like the best way, but this is actually horrible. Too many vibrations will break it quickly and too much work on assembly.
For this fast assembly iteration, I decided on the second option, clamping the motor mount to the axle. However, according to the eskateboard community, they break a lot. So I tried to fix those problems by using large three and a half inch screws that went through the entire 3D printed piece. They were in charge of reinforcing the motor mount to withstand vibrations, while also acting as the clamp to the actual axle.
Total Costs
Specs | Cost | Link |
---|---|---|
ESC-6S | $51.90 | HobbyKing |
Li-Po Battery | $23.45 * 2 | HobbyKing |
270Kv Motor | $53.40 | HobbyKing |
Remote Controller | $18.35 | Ebay |
Caliber Trucks | $35 | Amazon |
Wheels | $28 | Amazon |
Board | $37 | Amazon |
BMS (This one might've been faulty) | $15 | Ebay |
Timing Belt | $14.00 | Amazon |
Spacers | $7.99 | Amazon |
BESC programming card | $7.55 | Hobby King |
Screws (1/4-20, 3 1/2" x 6), (10-32, 3 1/2" x 4), (2-56 set screws) and hex nylon lock nuts (1/4-20 x 6) | $5.00 at your nearest hardware store | Hardware store |
A small plastic box | $3.50 at your nearest hardware store | Hardware store |
XT-60 connectors | $8.99 | Amazon |
Voltage checker | $6.99 | Amazon |
24V Battery Supply | $9.99 | Amazon |
Total | $349.56 (PHEW!) |
Tools required
- Tap and Drill for 1/4-20, 2-56, and 10-32
- A hand-drill
- Countersink
- Soldering iron
- Electrical tape
The Circuit
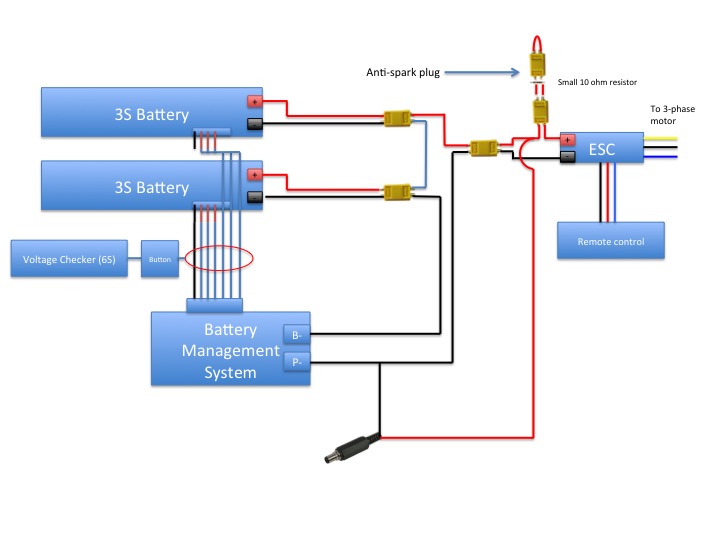
You then buy a Battery Management System (BMS) that is also specced for 6S and a discharge rate of ~45A and a pulse rate of at least 60A. The Battery Management System allows you to charge the LiPo batteries one cell at a time, which increases lifetime and prevents the battery from bursting into flames. Having an internal BMS also allows you to easily charge the battery with just a DC jack rather than using conventional methods of charging each 3S battery separately with a balance charger.
To check the battery level, we have a voltage checker which reads out the voltage of the individual batteries. This allows us to continuously check that the BMS is working, but because we don't always want to check, we have a button that we press to turn it on.
Lastly, we have an anti-spark plug that turns on the ESC. The anti-spark plug catches the spark that happens with you connect a high voltage to a free line. If you don't suppress the spark, the connection with begin to oxidize and it'll eventually oxidize to the point of high resistance and difficulty plugging in and out. We use two XT-60 connectors, one that connects with a 10ohm resistor, and the other that is free. The 10 ohm resistor catches the spark, and then plugging in the other XT-60 allows for the circuit to take the path of least resistance away from the 10ohm resistor.
Design decisions
Actual Skateboard
I bought Caliber trucks, which are incredibly high quality trucks for the price. They have rectangular axles, which allow for you to clamp the motor mount on them.For the board, we bought this. Doug definitely wanted something cooler, but because we were price constrained, we chose something cheap.
Motor, Batteries, and ESC
I used this to to figure out I needed a solid 18mph ratio (you can use an efficiency of 60%). I added 6S batteries on a 270 kV motor, with a 28-teeth small pulley and a 56-teeth large pulley (reasons for that explained later).I used that particular ESC because it was the cheapest and most versatile high voltage ESC for its price. Because the discharge of the motor was maxed at 60A, but ESCs have a tendency to break very quickly, I overspecced for 100A. It worked like a charm.
Belt Decisions
I chose GT3 belts because backlash upon stopping is better than the trapezoidal timing belt system in HTD belts. I chose GT3 instead of GT5 because the load is spread more across the entire pulley, which is essential for 3D printed parts, and there were cheap GT3 Boosted Belt replacement belts that we used. I needed to maintain a reasonable distance between the large pulley and the small pulley, which ended up being a mere 7mm. Problems occurred later with the shaft of the motor interfering with the wheel, but we fixed that. Use this website to help with calculations.Battery Management System and Voltage Checker
We got this beeper to give us accurate battery measurements. The BMS we bought might've been faulty, because when we plugged in our batteries, they were discharging rapidly. We still have to figure out the issue.Motor Mount
The motor mount went through a lot of iterations. We eventually ended up with the one you can see below.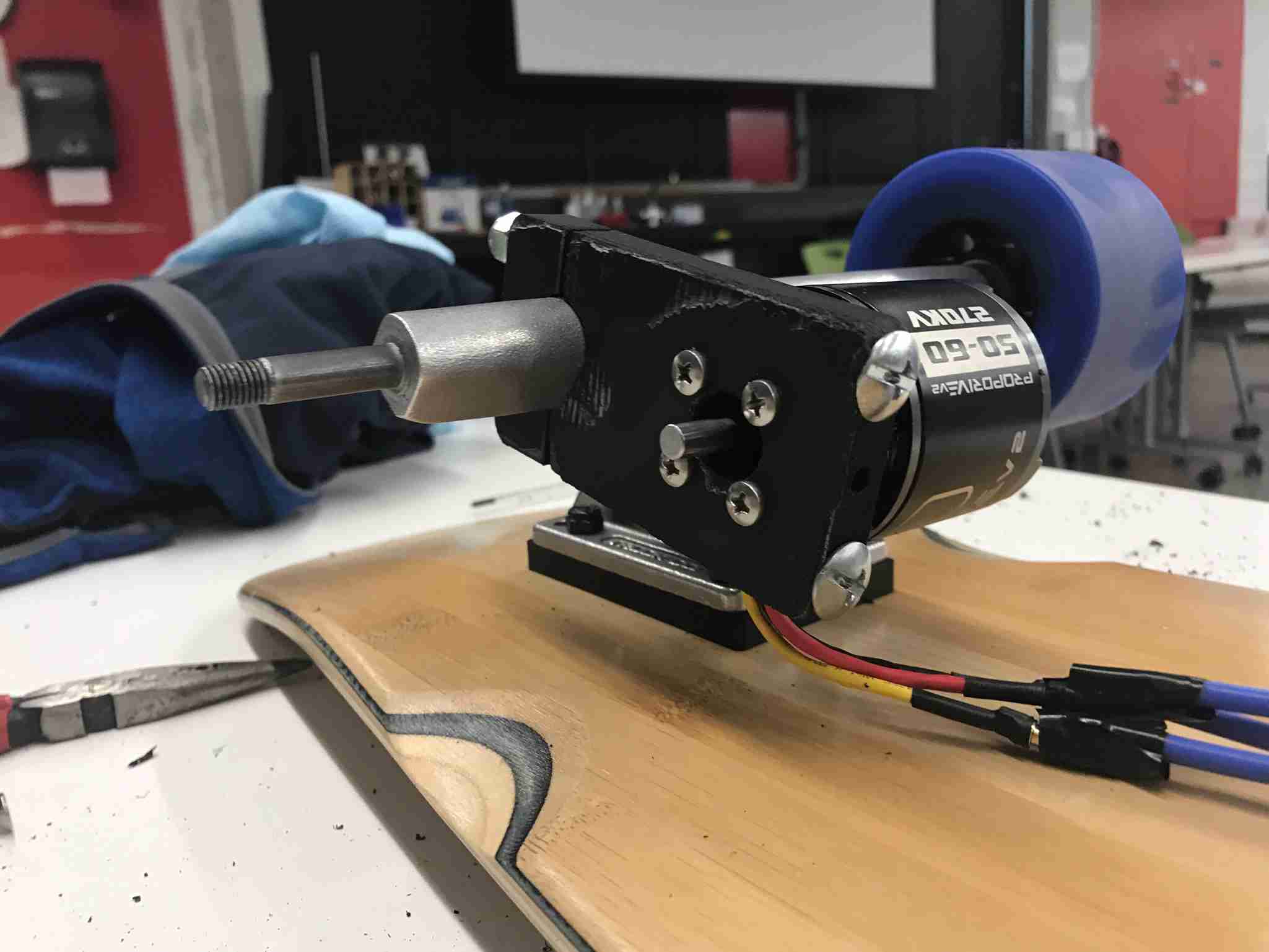
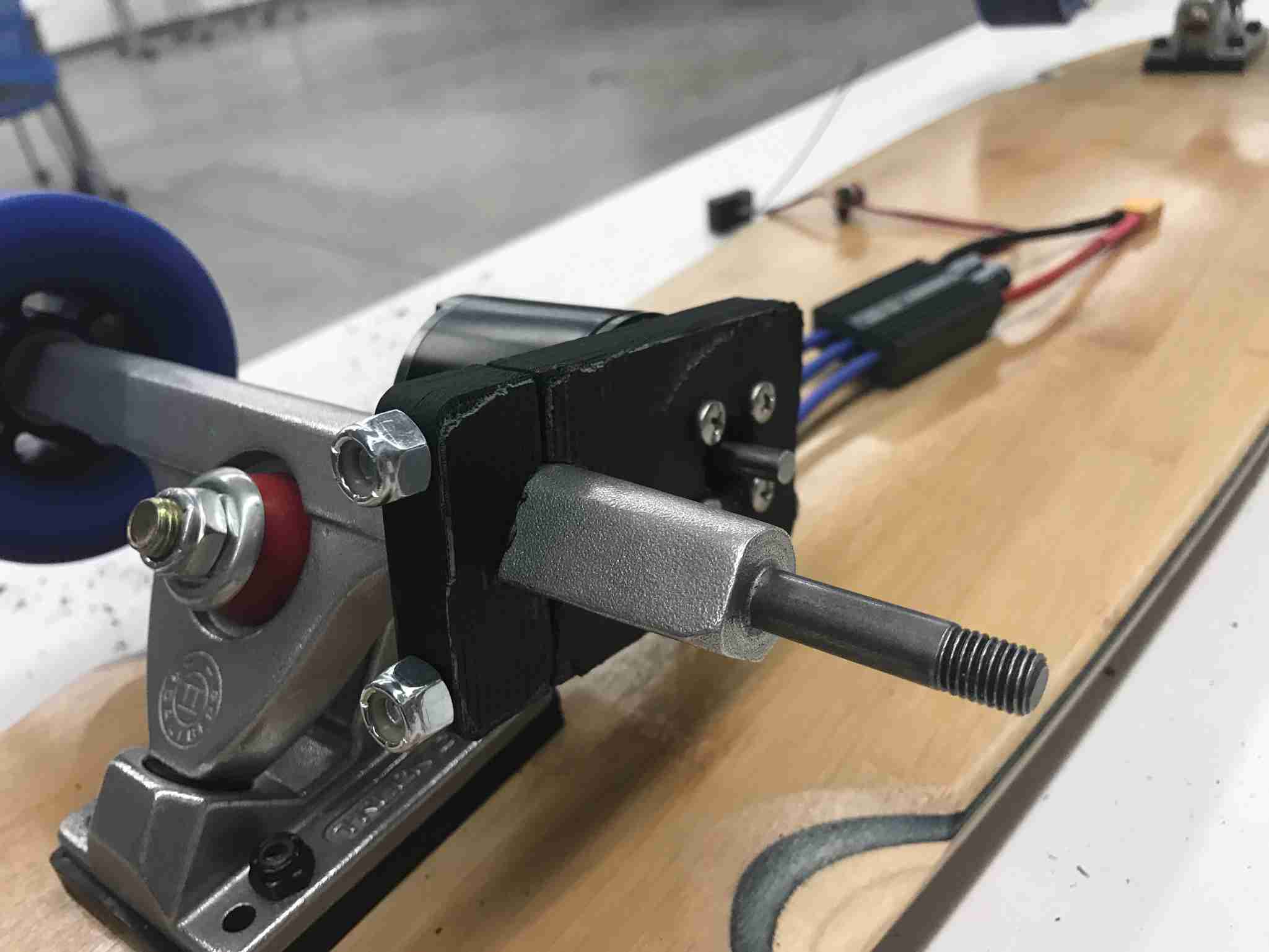
The idea was to strengthen the mount against vibrations. We cut two tight fit holes in the larger half of the motor mount and then one tapped hole in the smaller half. Then, we tapped the smaller half with a 1/4-20 tap and used a clamping mechanism. In essence, we use the versatility of 3D printing while enfusing it with the strength properties of the steel. Vibrations of the motor are now securely transferred to the axle, and vibrations different terrain cannot break the 3D print as it would also need to bend the steel screw.
Remote Controller
I used this very simple and durable remote controller. Those that were meant for RC cars were too bulky, but this one was just perfect. It also used adaptive frequency hopping, which was very helpful. Do not use the NRF24L01 for reliable and on-time data transmissions.Power Supply for Battery Charging
You can easily find these power supplies lying around, but I provided a link to be sure. You should technically go up to 25.2V for LiPo batteries to maximize the battery, but I couldn't find one in the price range we wanted. In all honesty, going through a garage sale will probably land you a solid 25.2 or 24V power supply very easily. The difference per cell is also only .2V per cell, which is around a 10% reduction in battery life.Building the actual skateboard
Putting together the skateboard
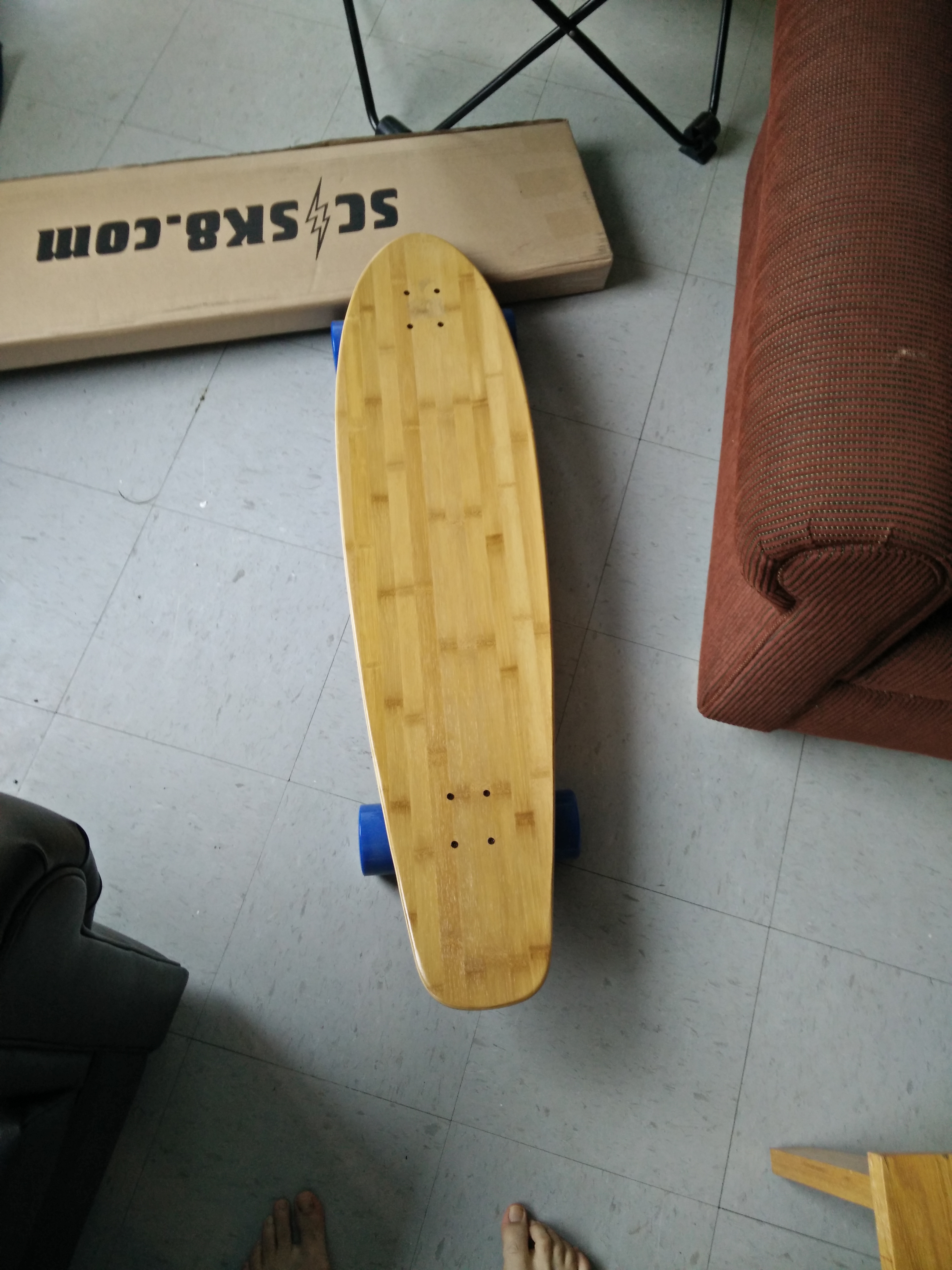
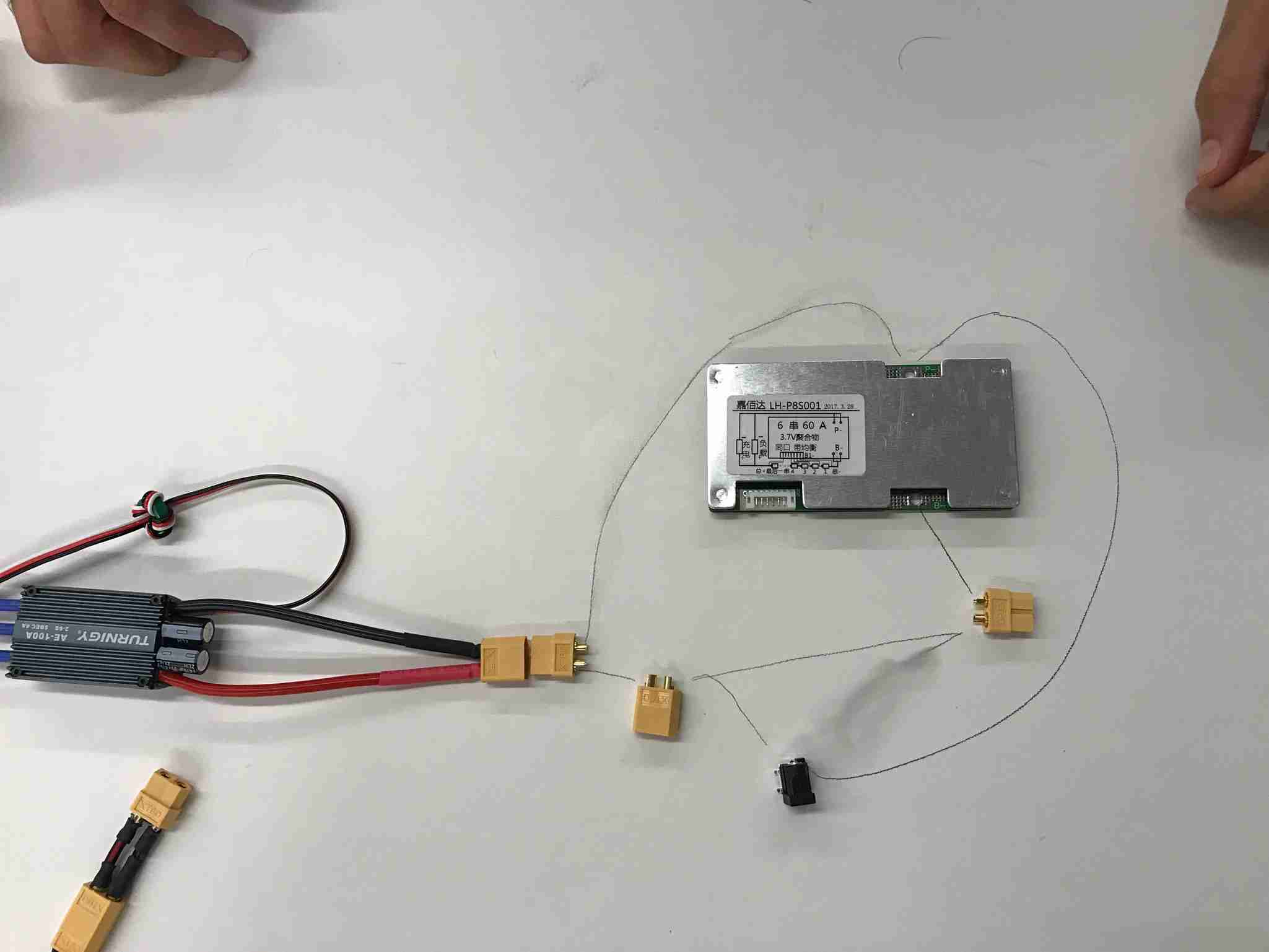
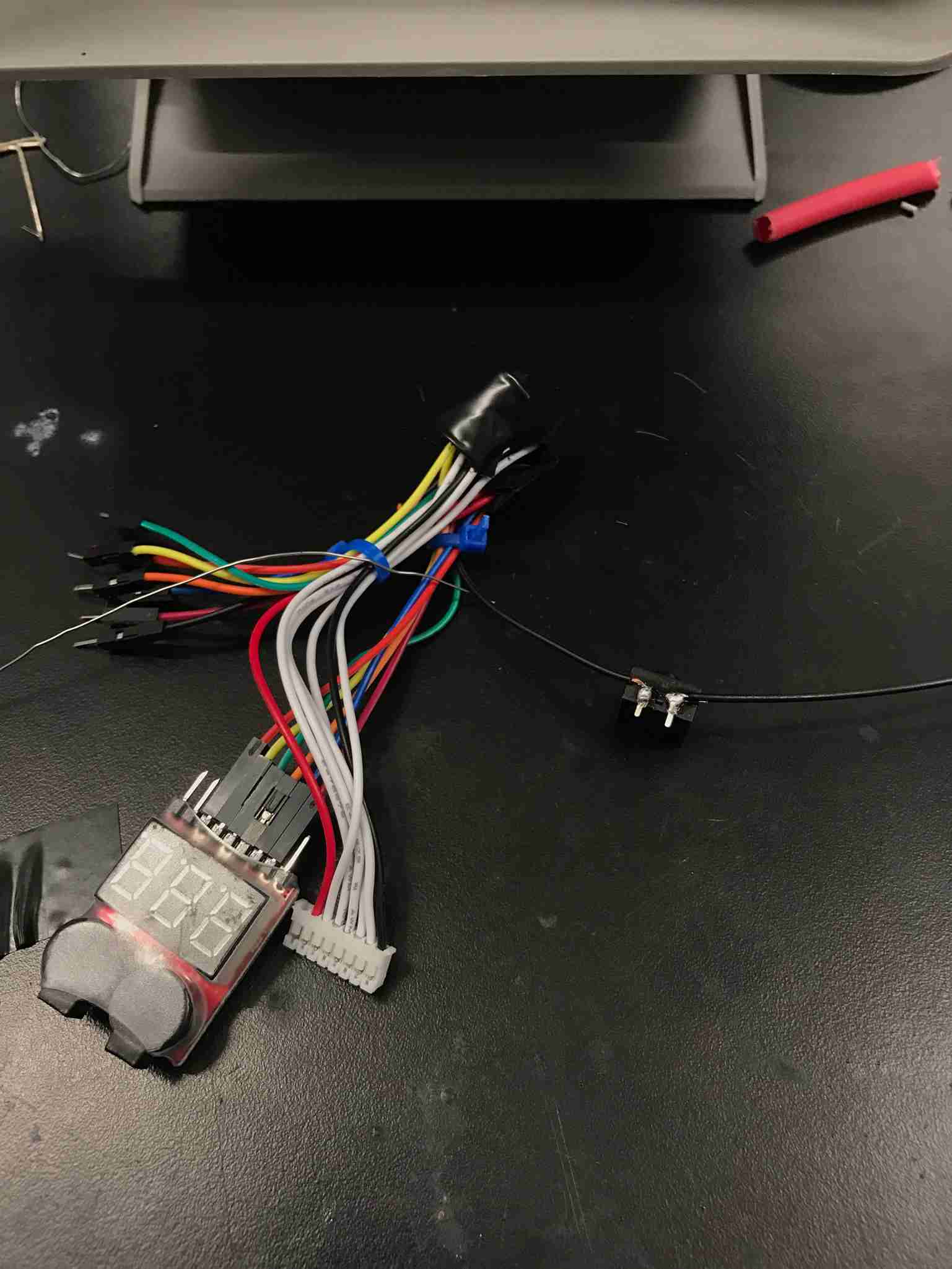
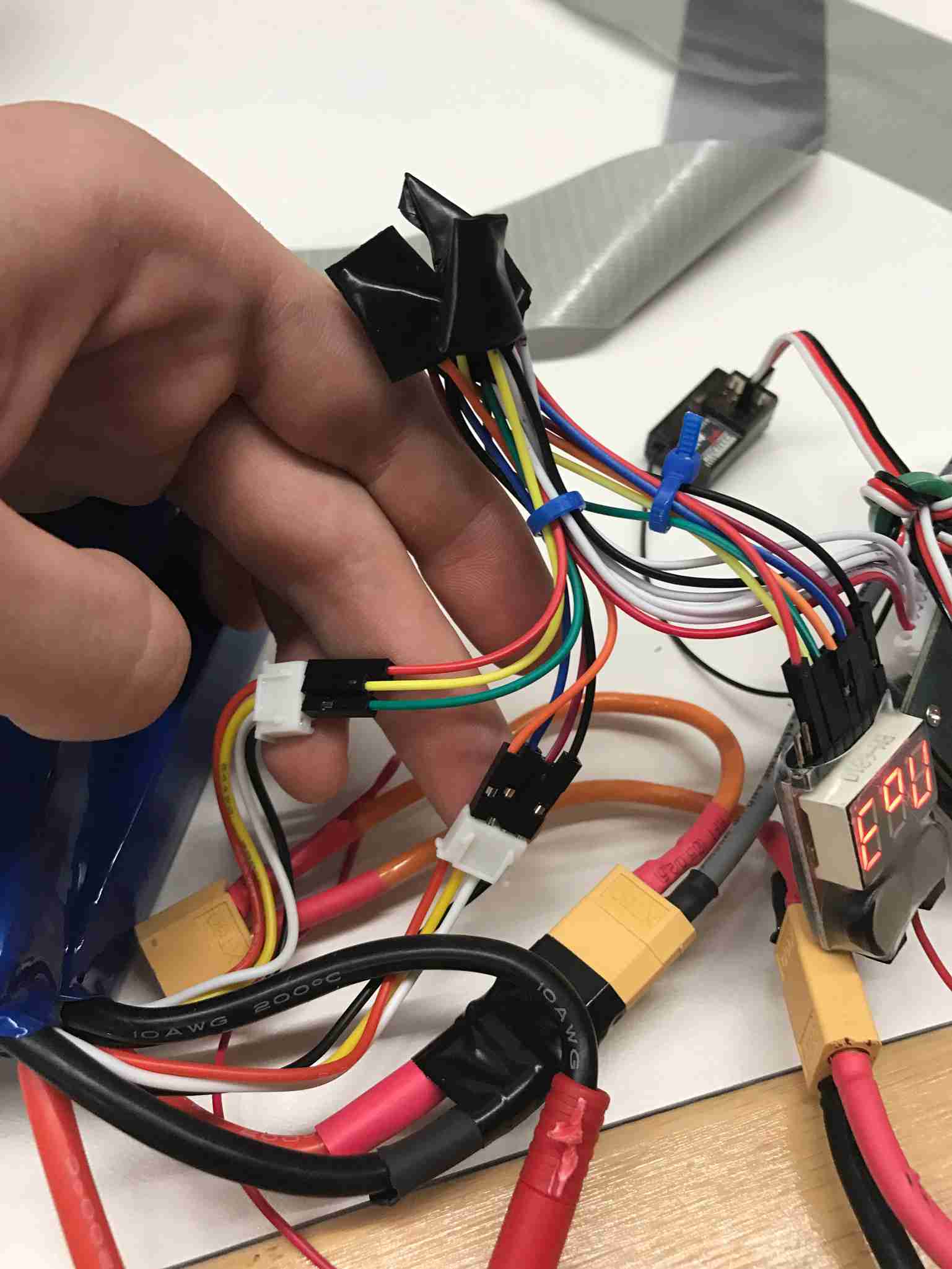
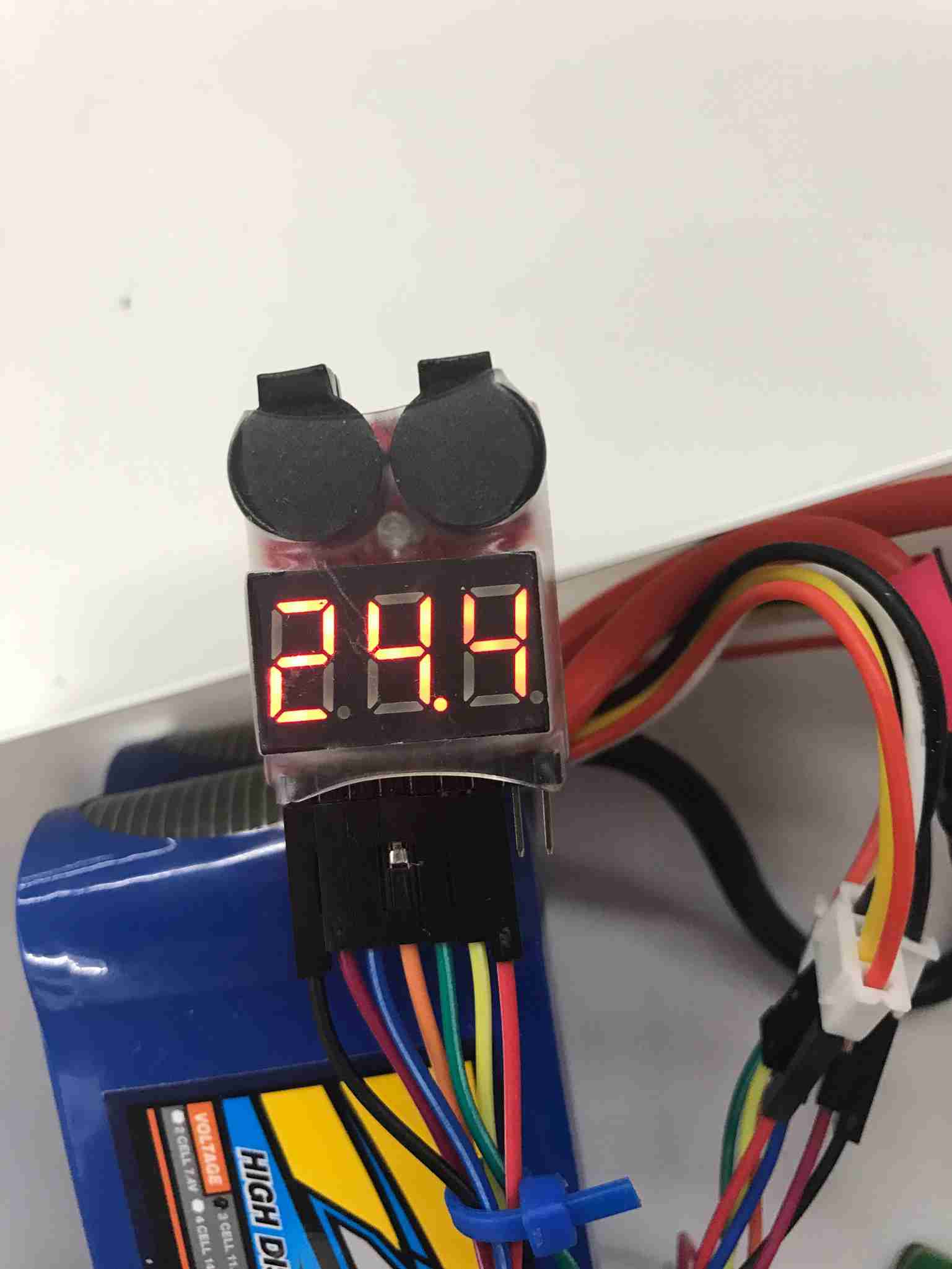
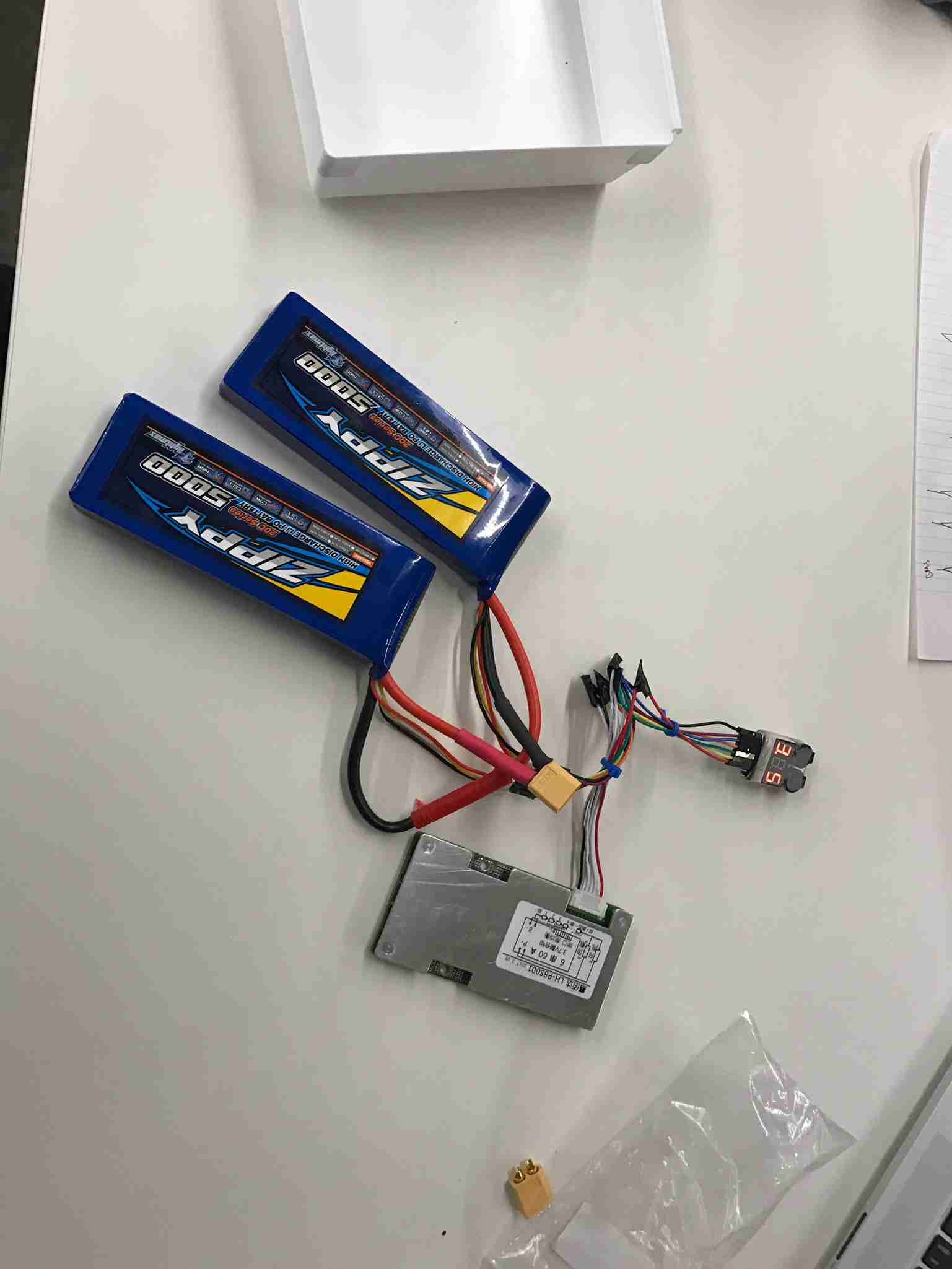
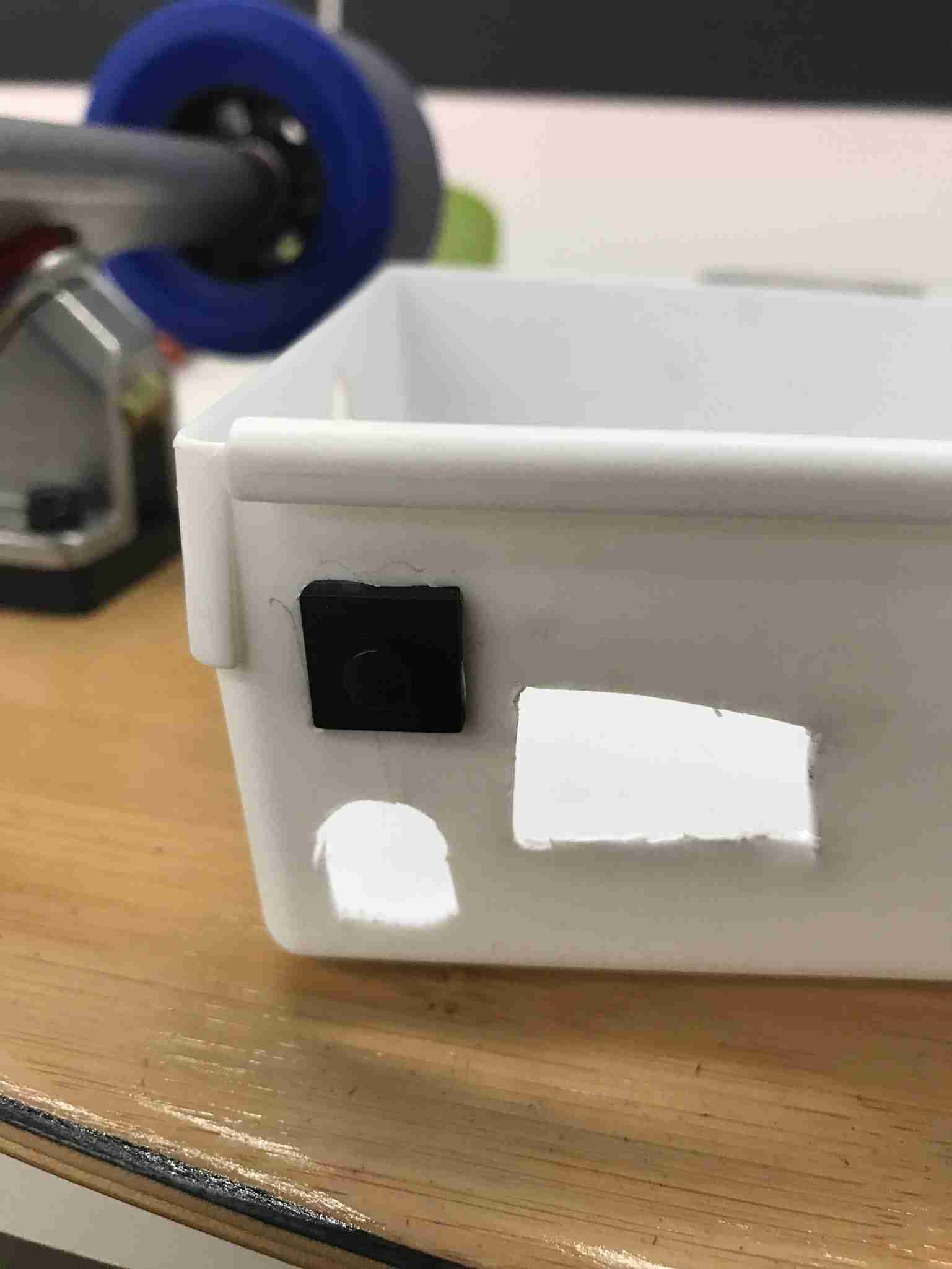
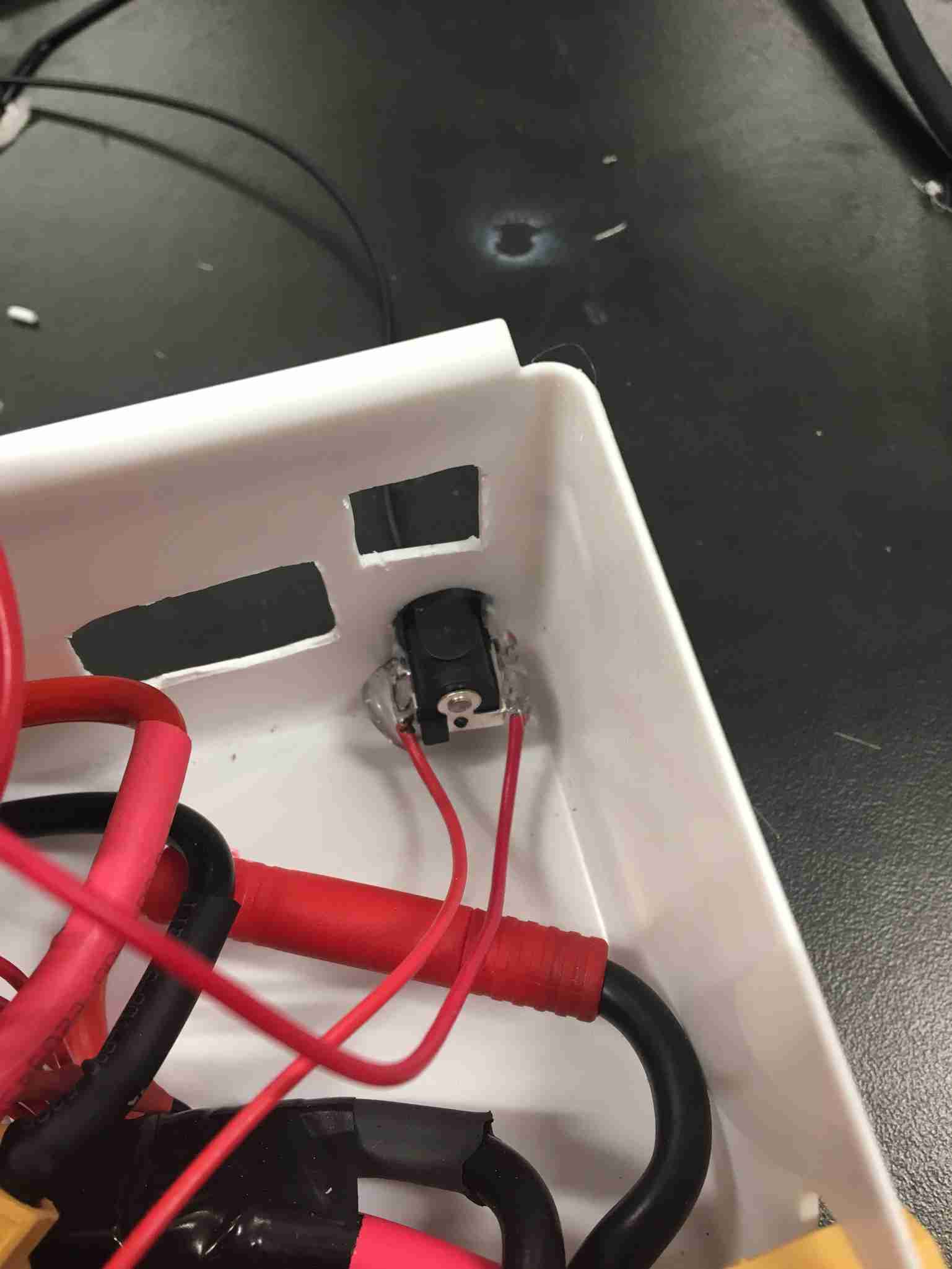
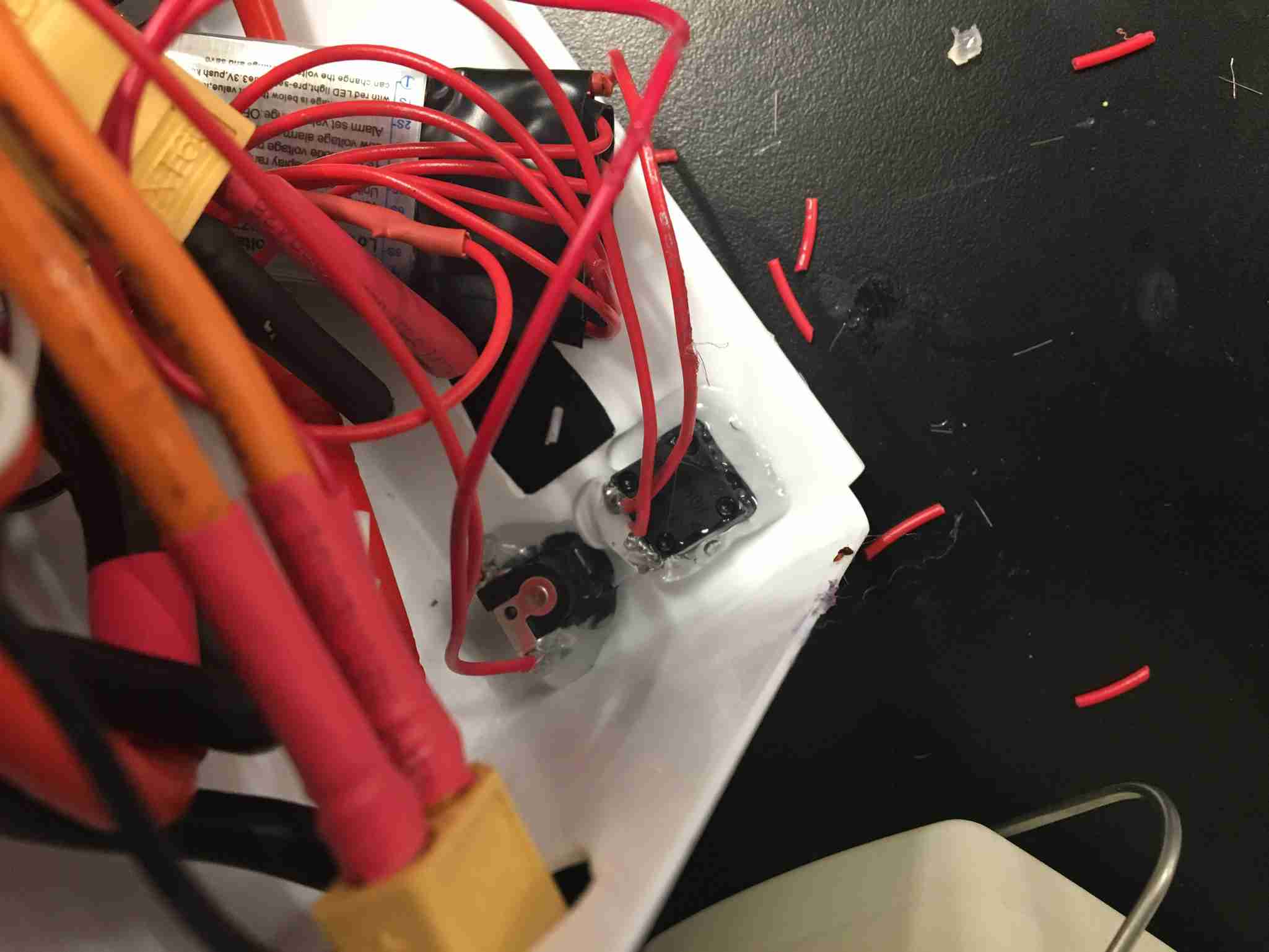
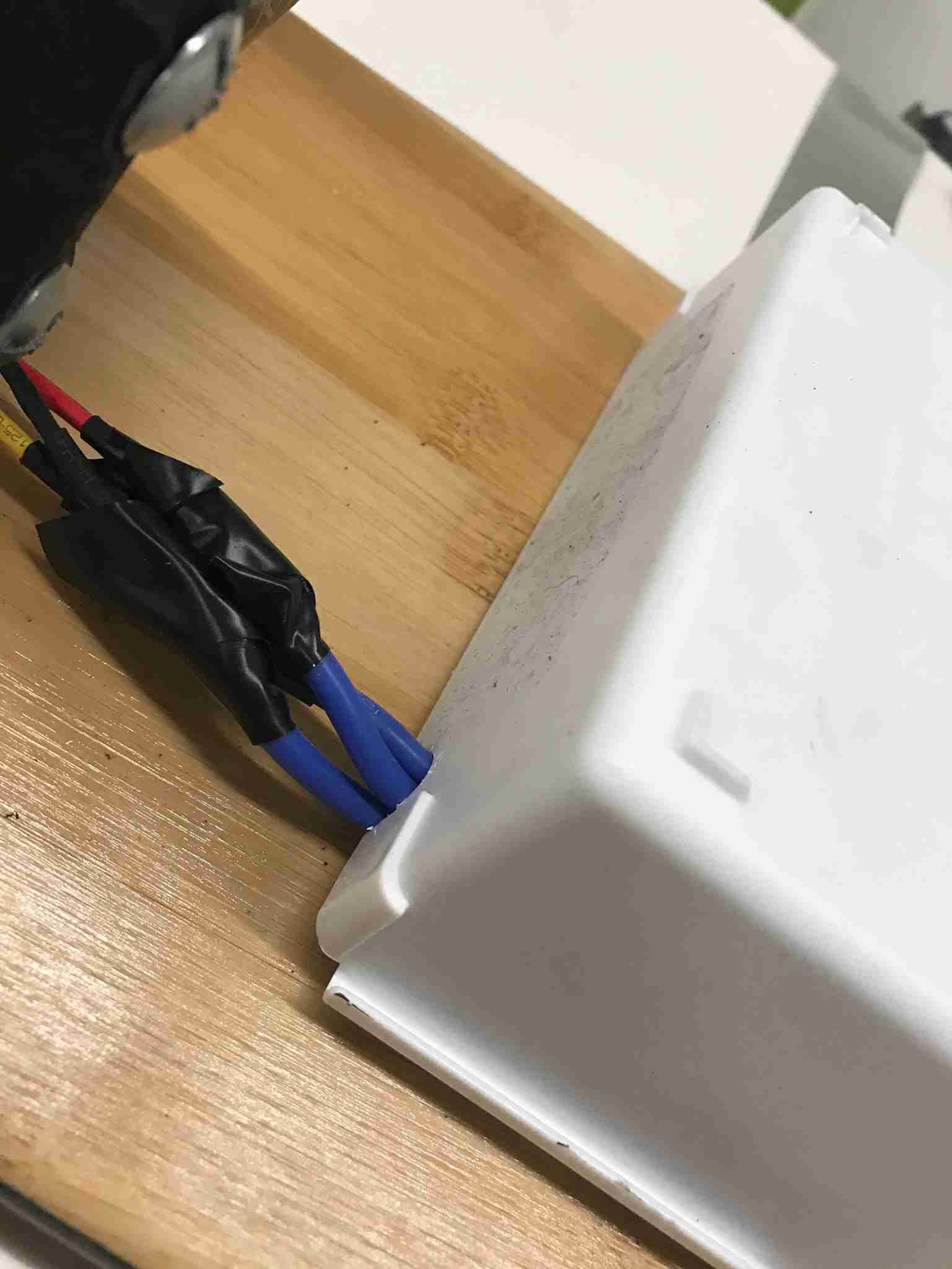
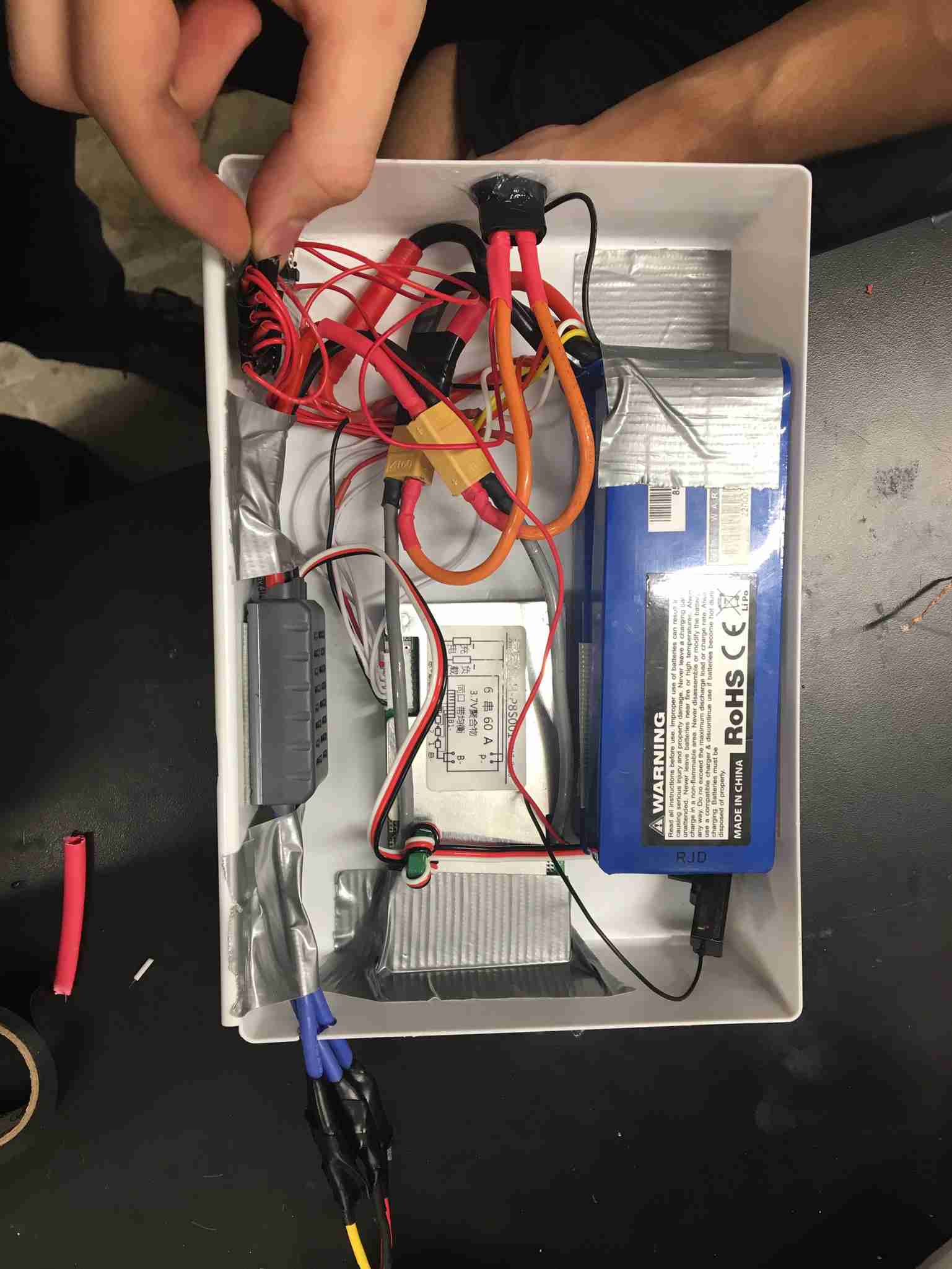
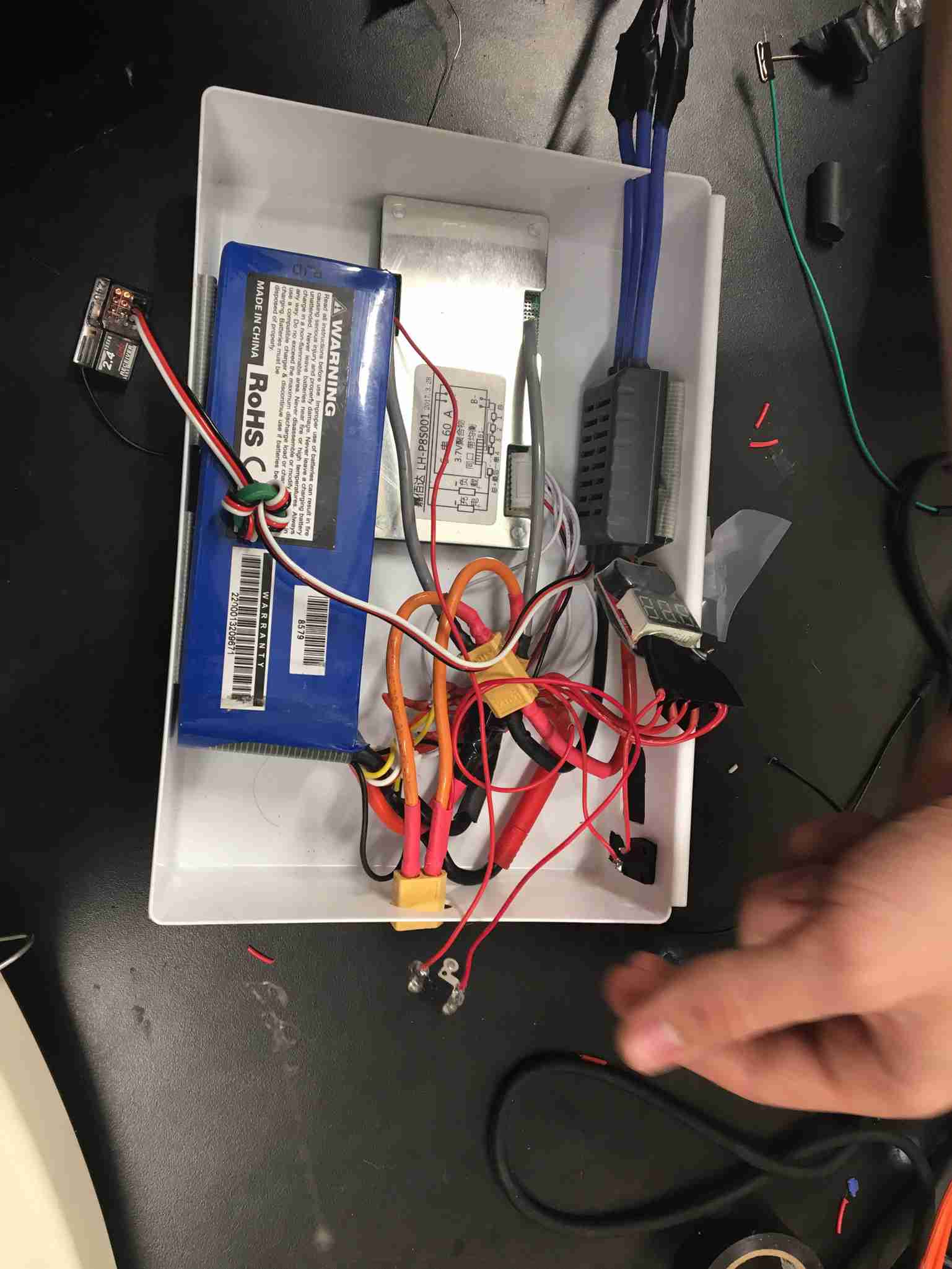
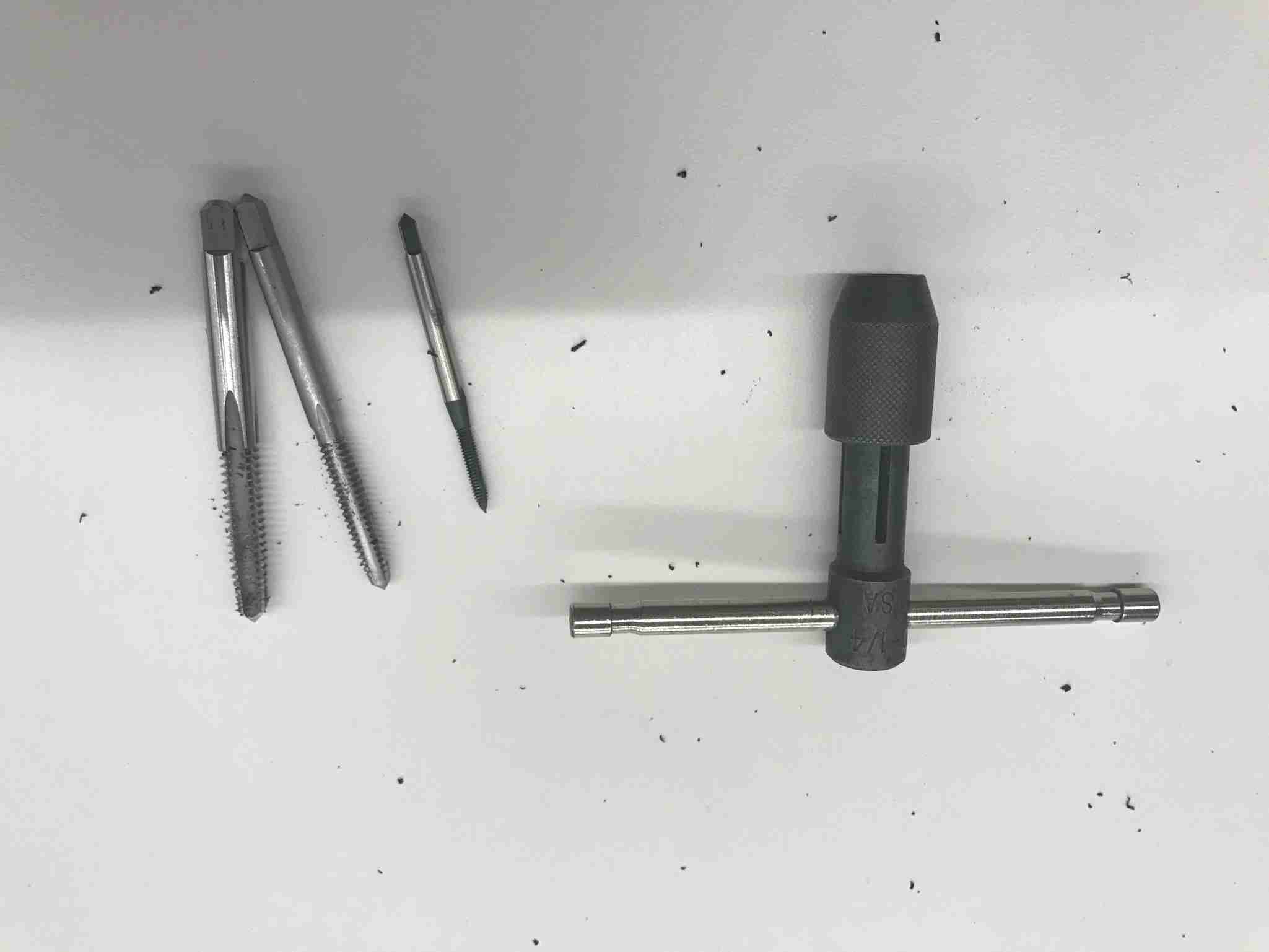
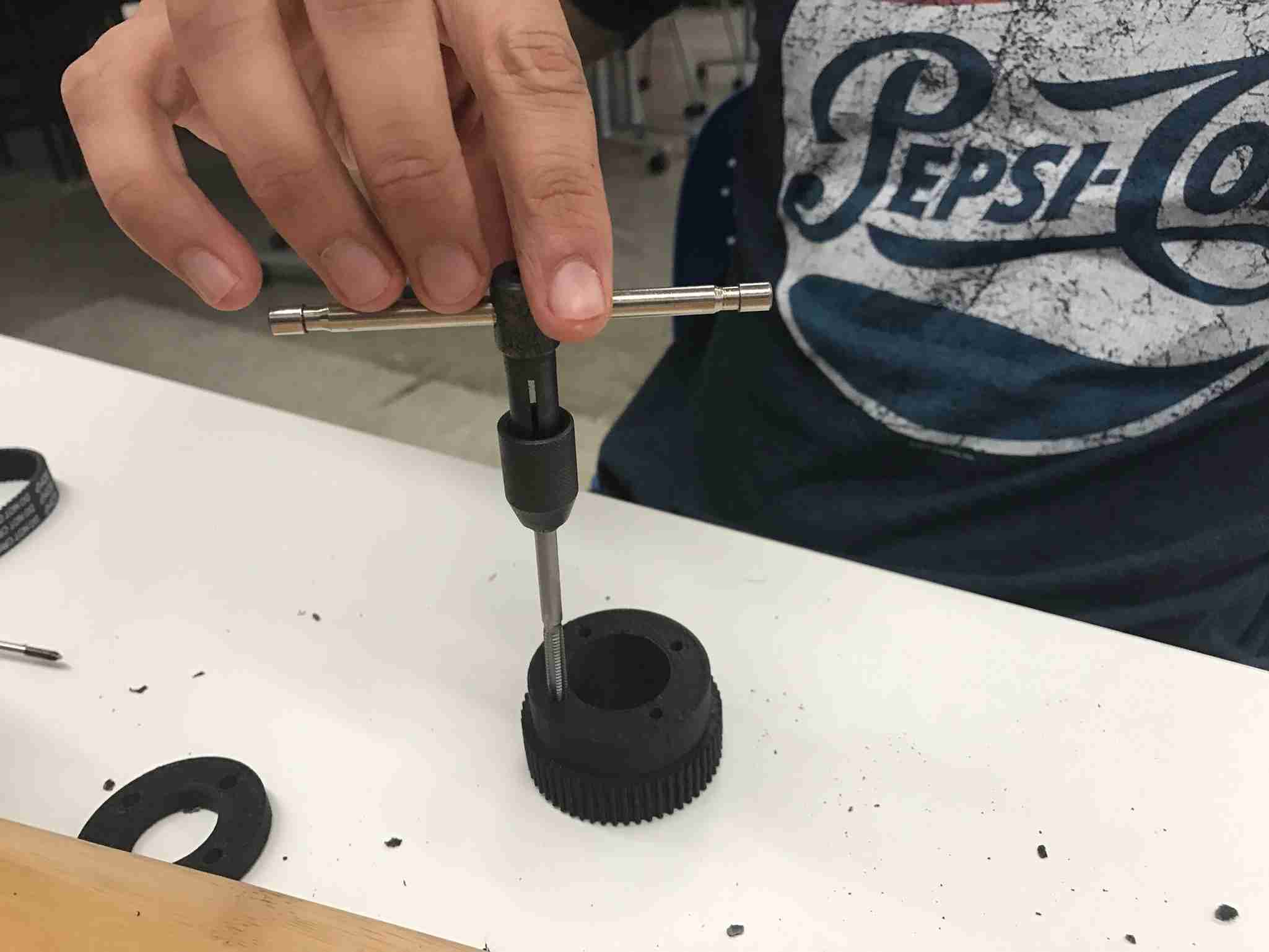
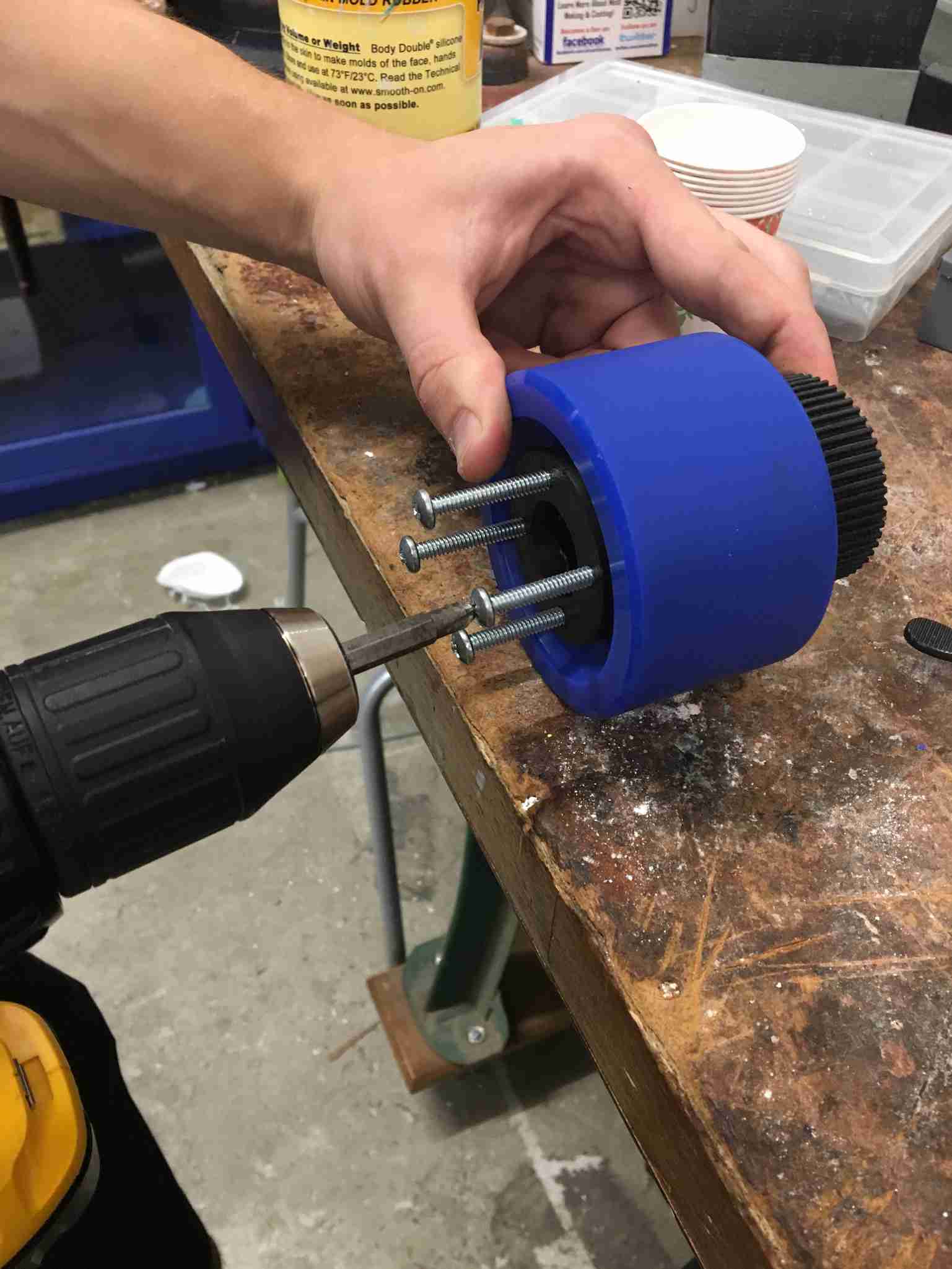
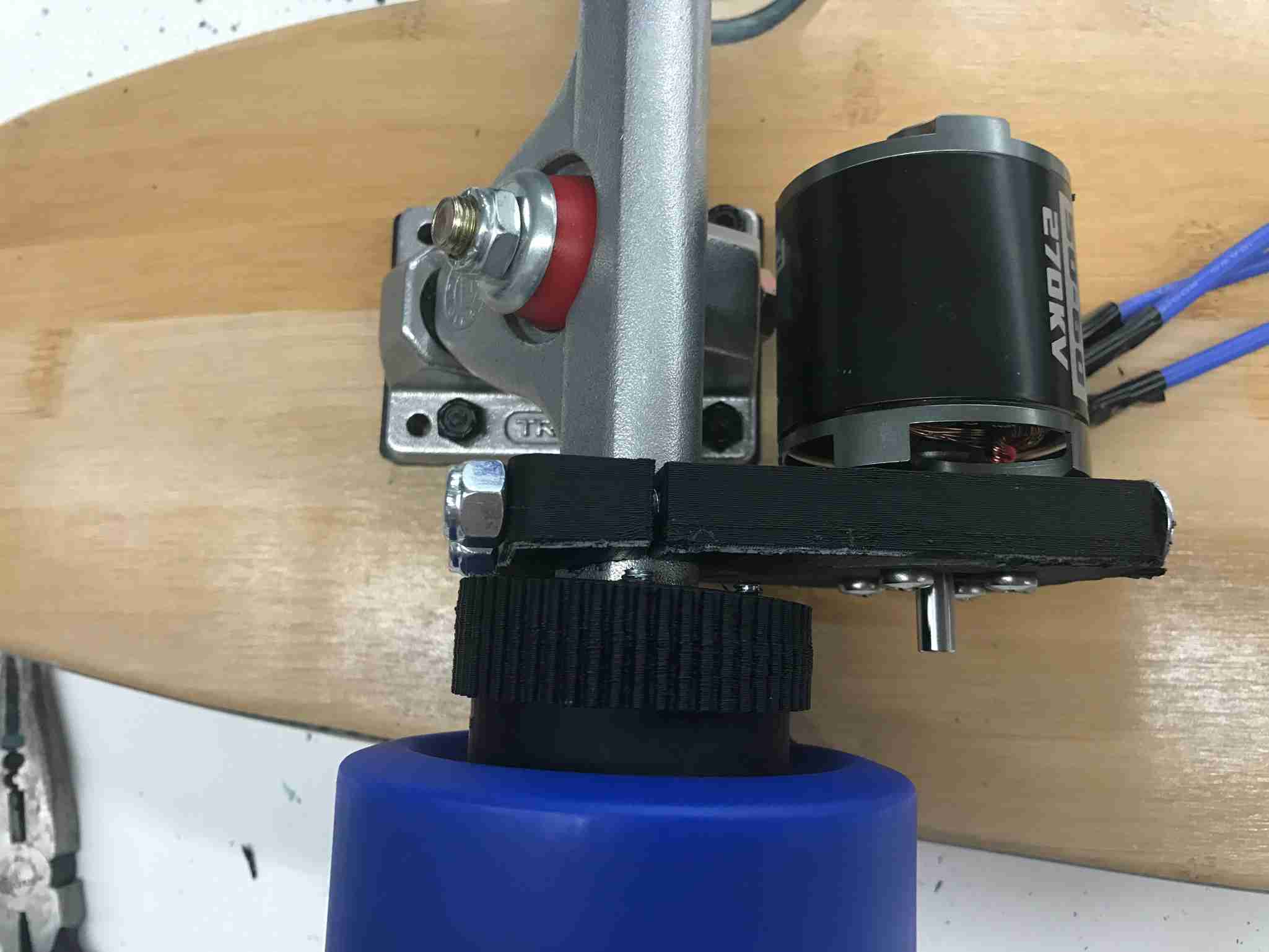
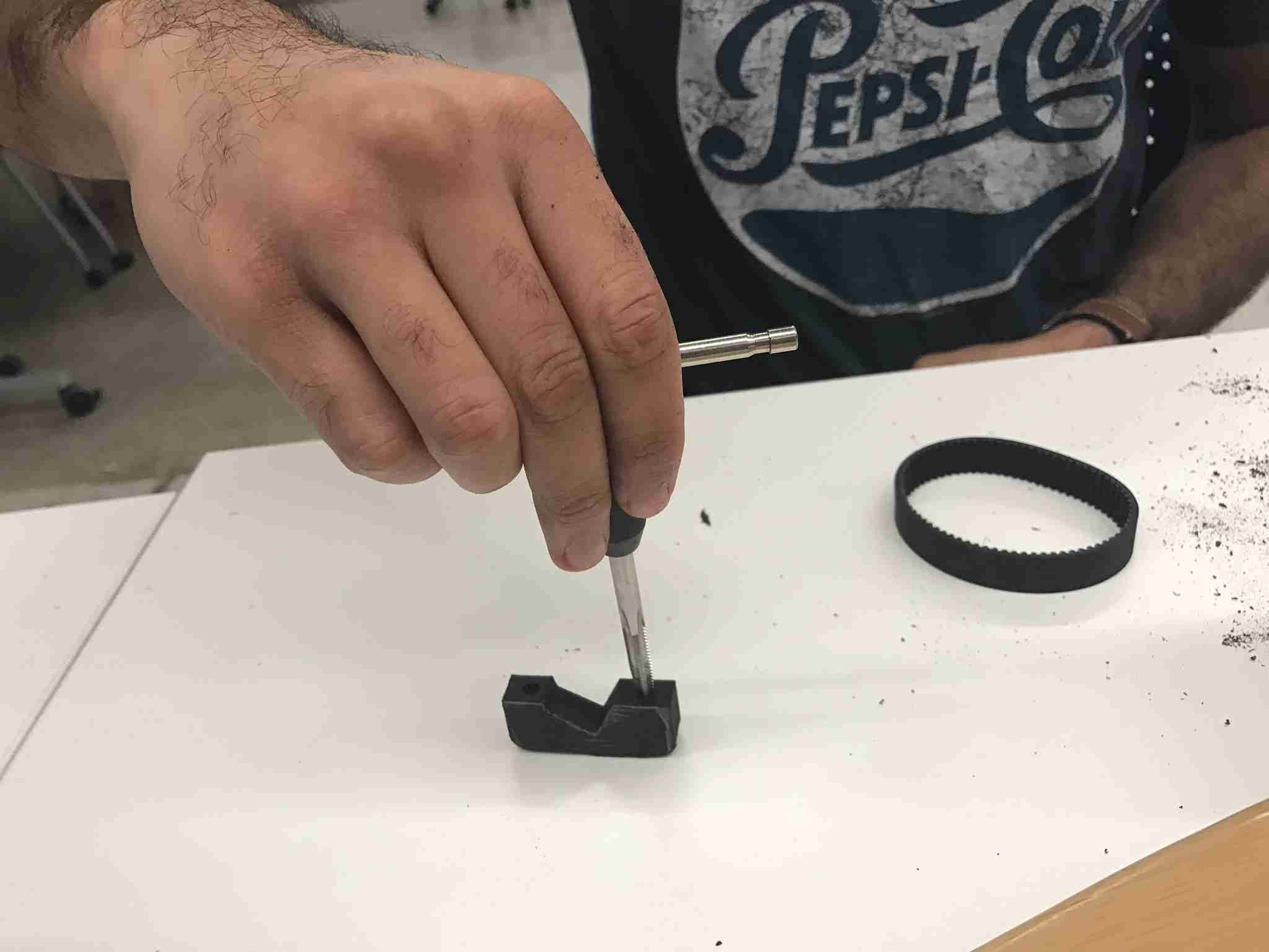
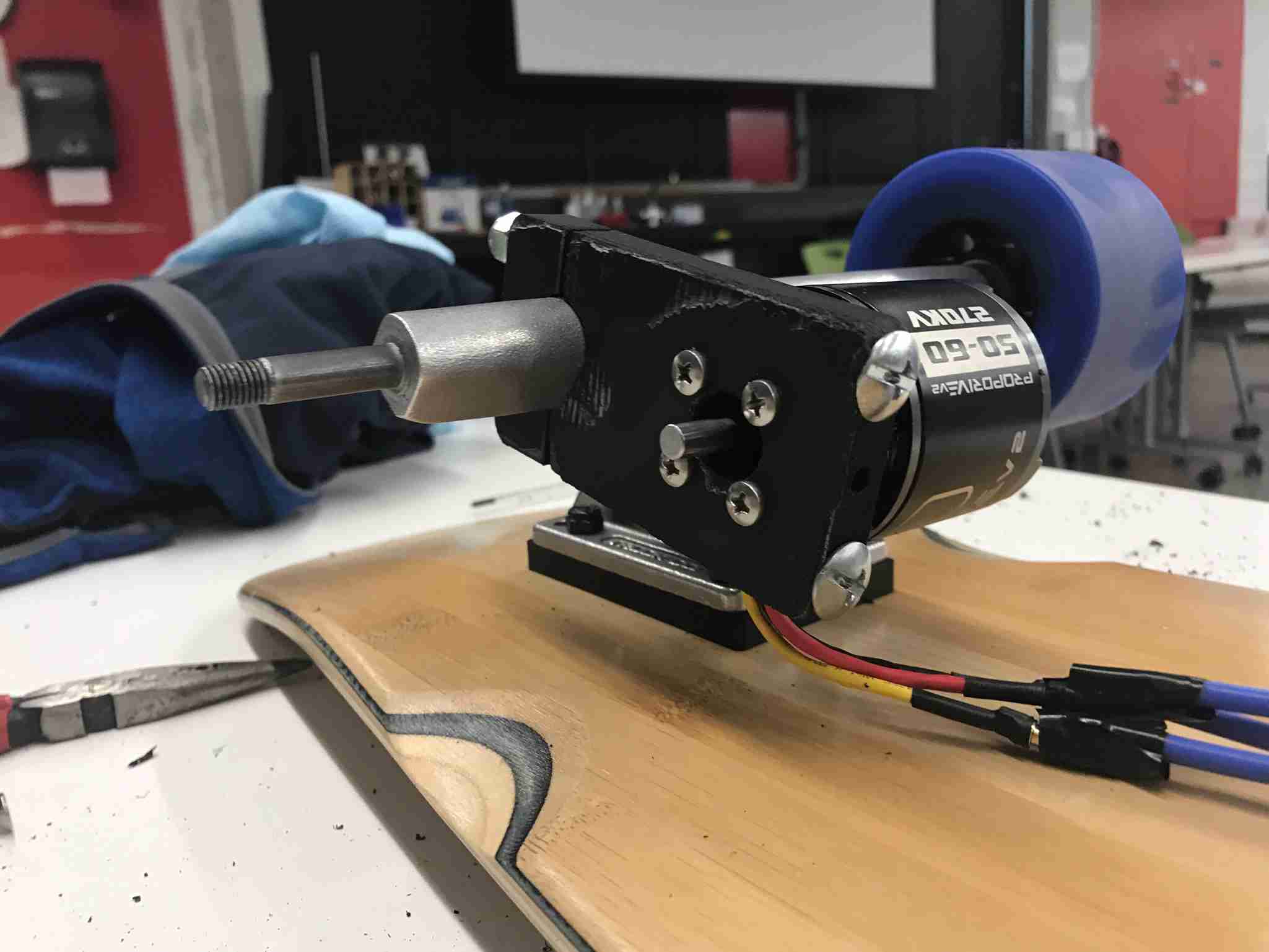
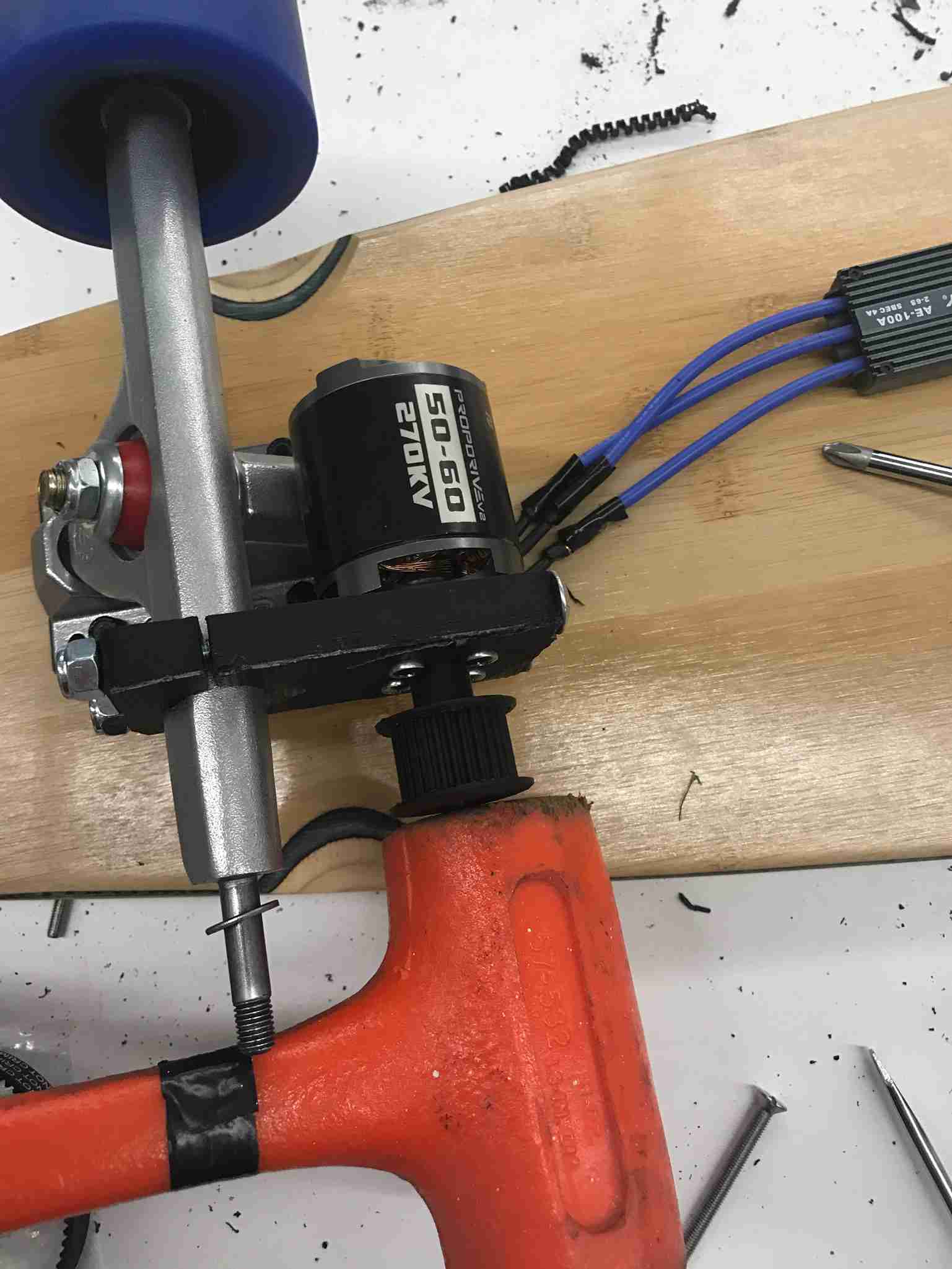
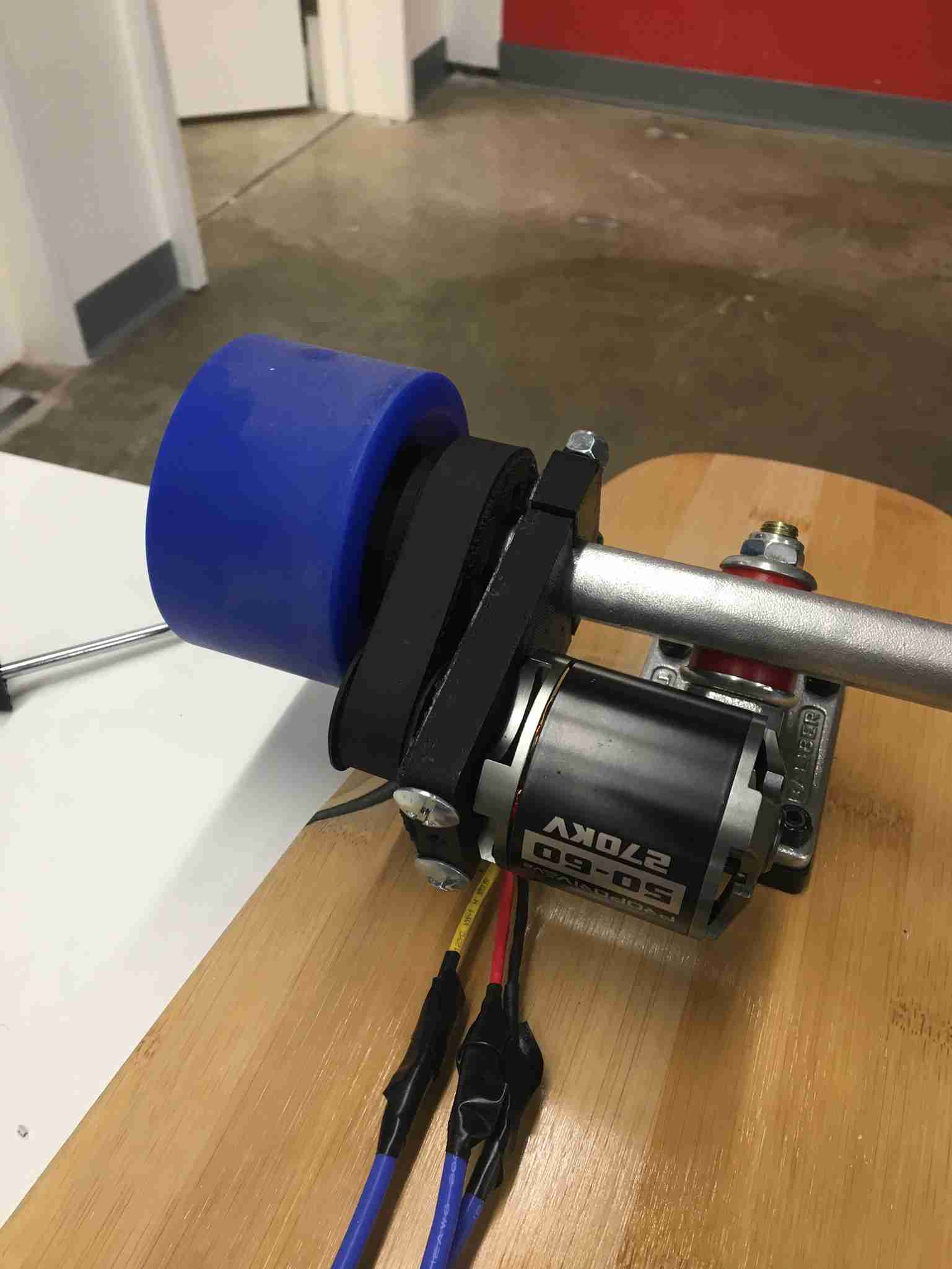
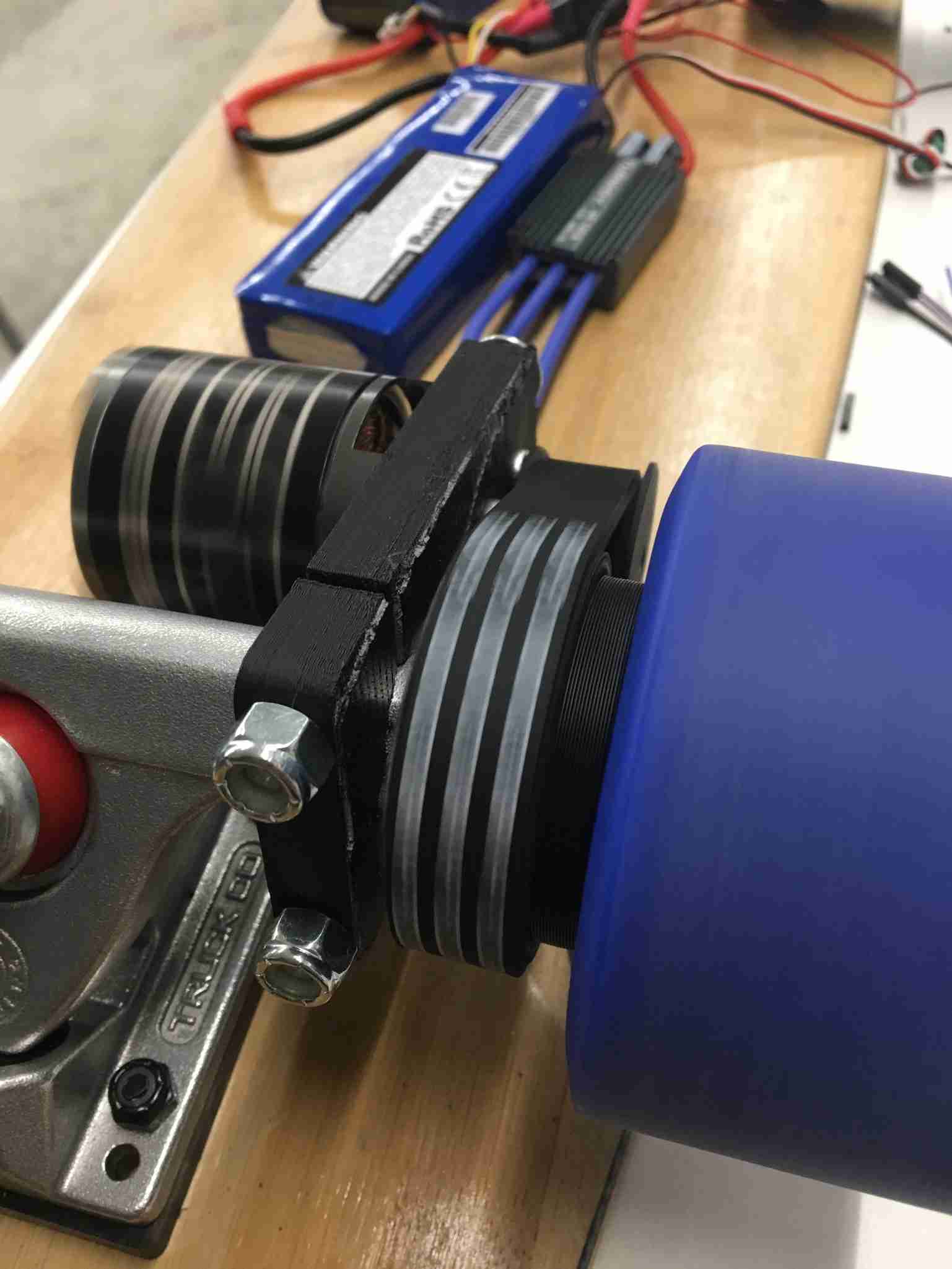
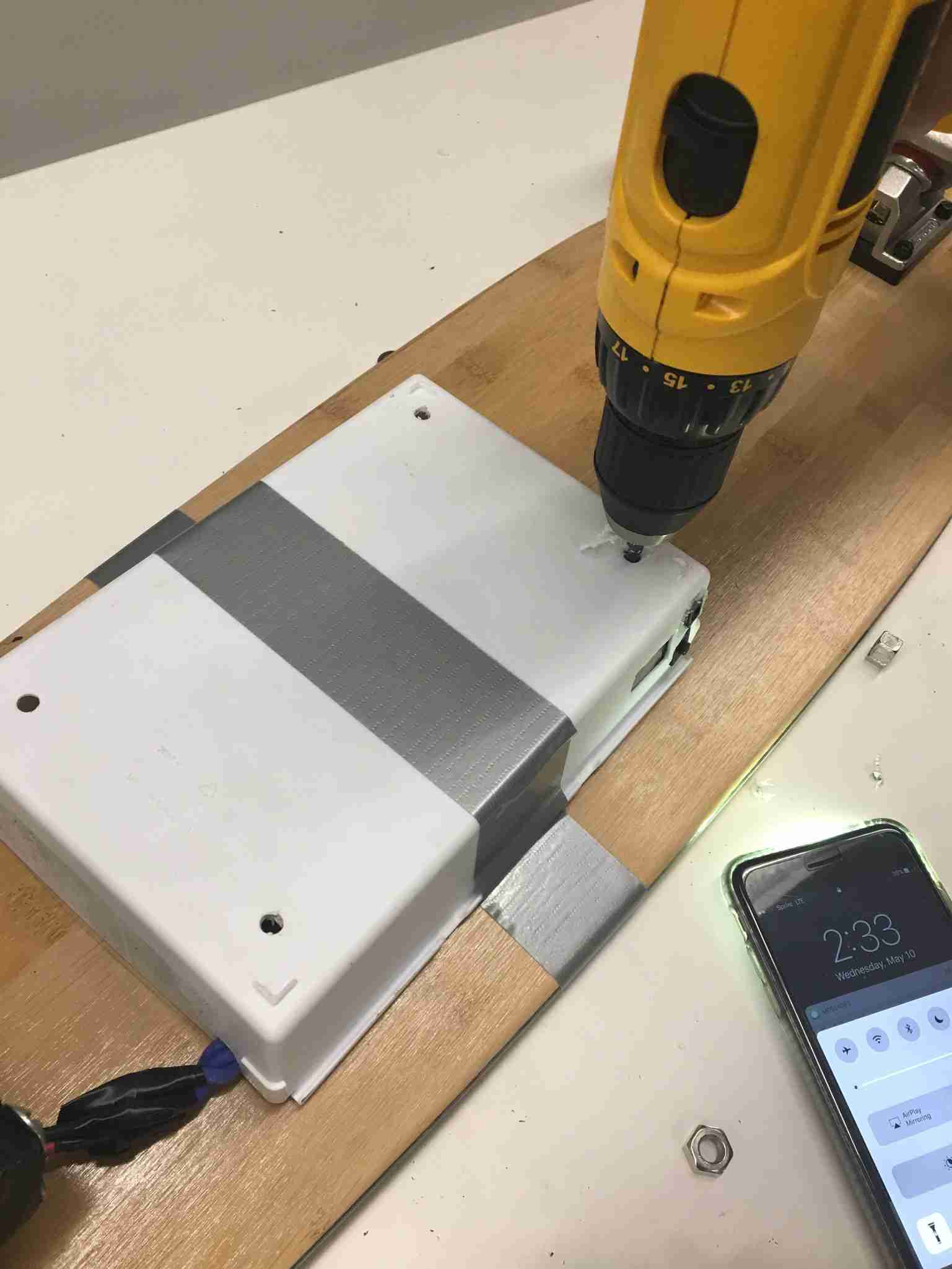
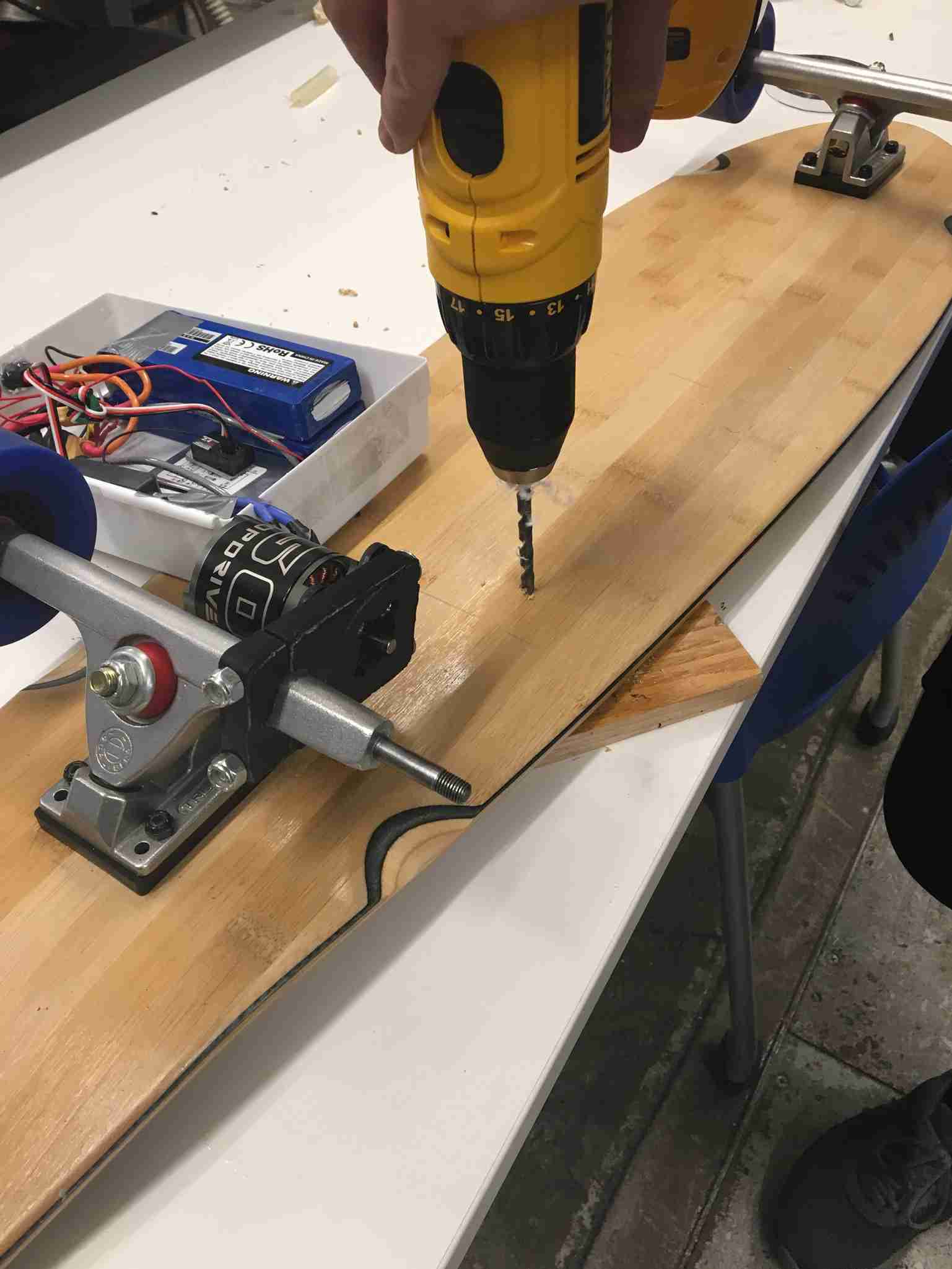
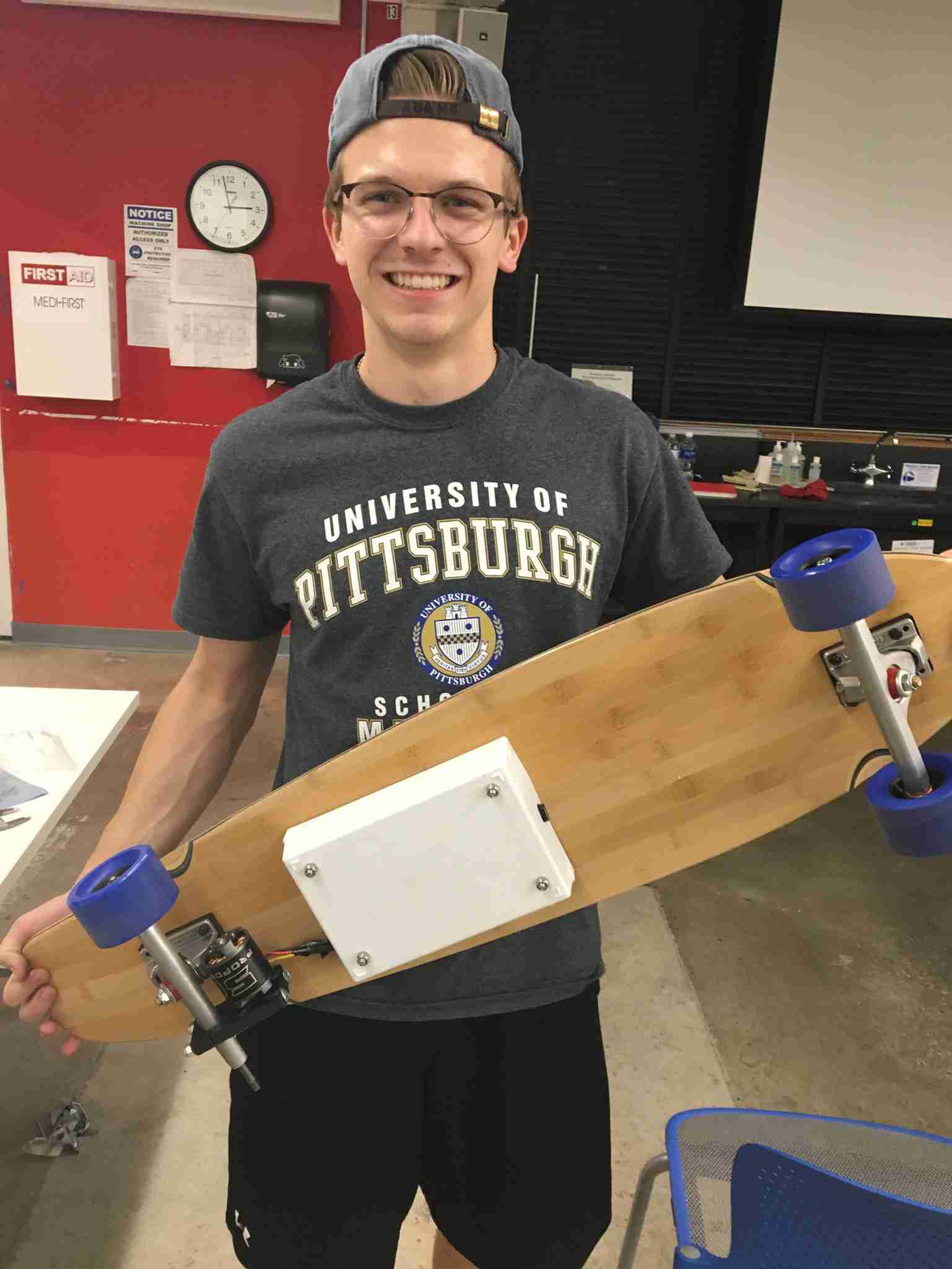
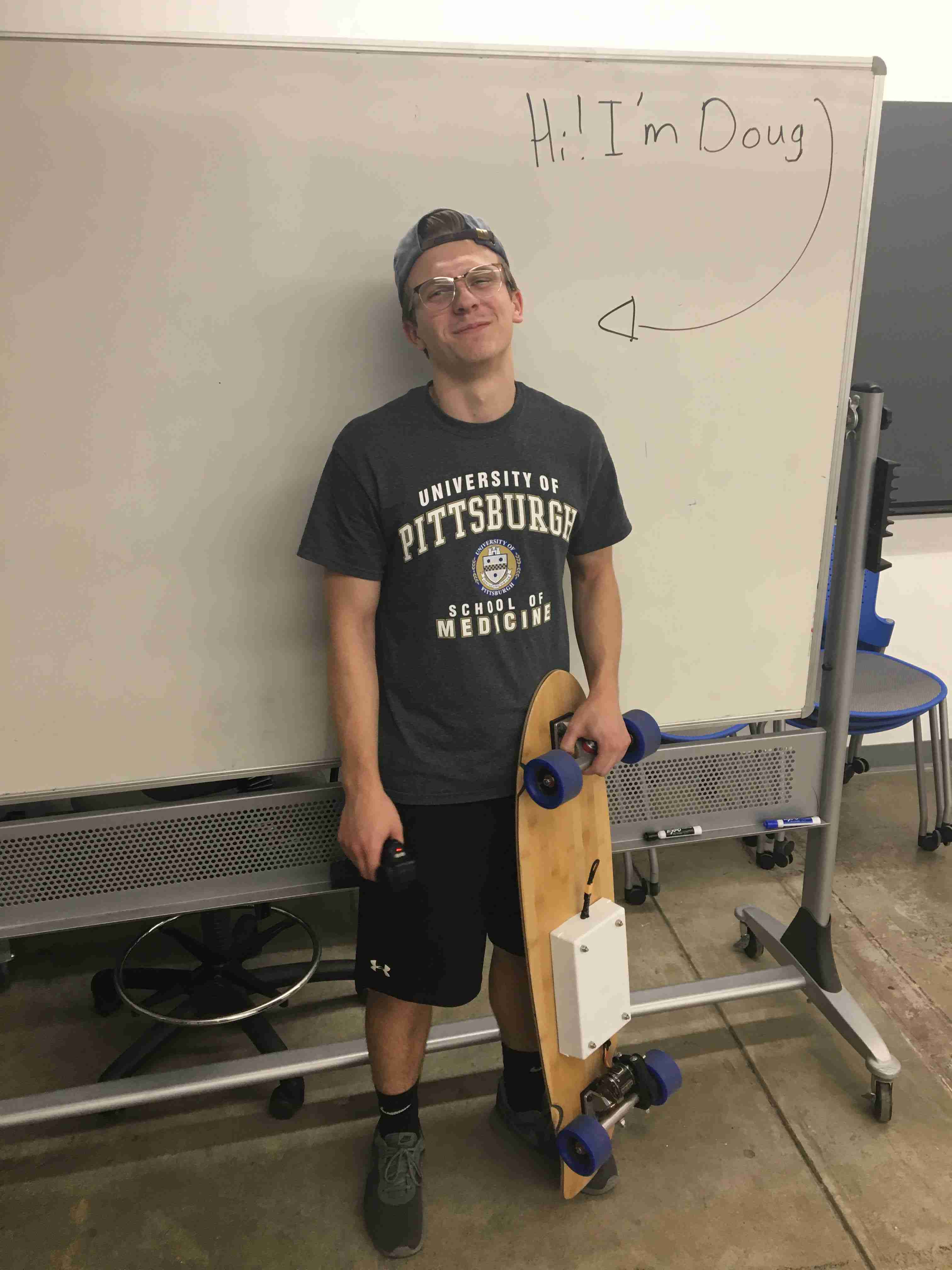